Tg point of PCB - the universal error in Rework Process. That error must / can be avoided.
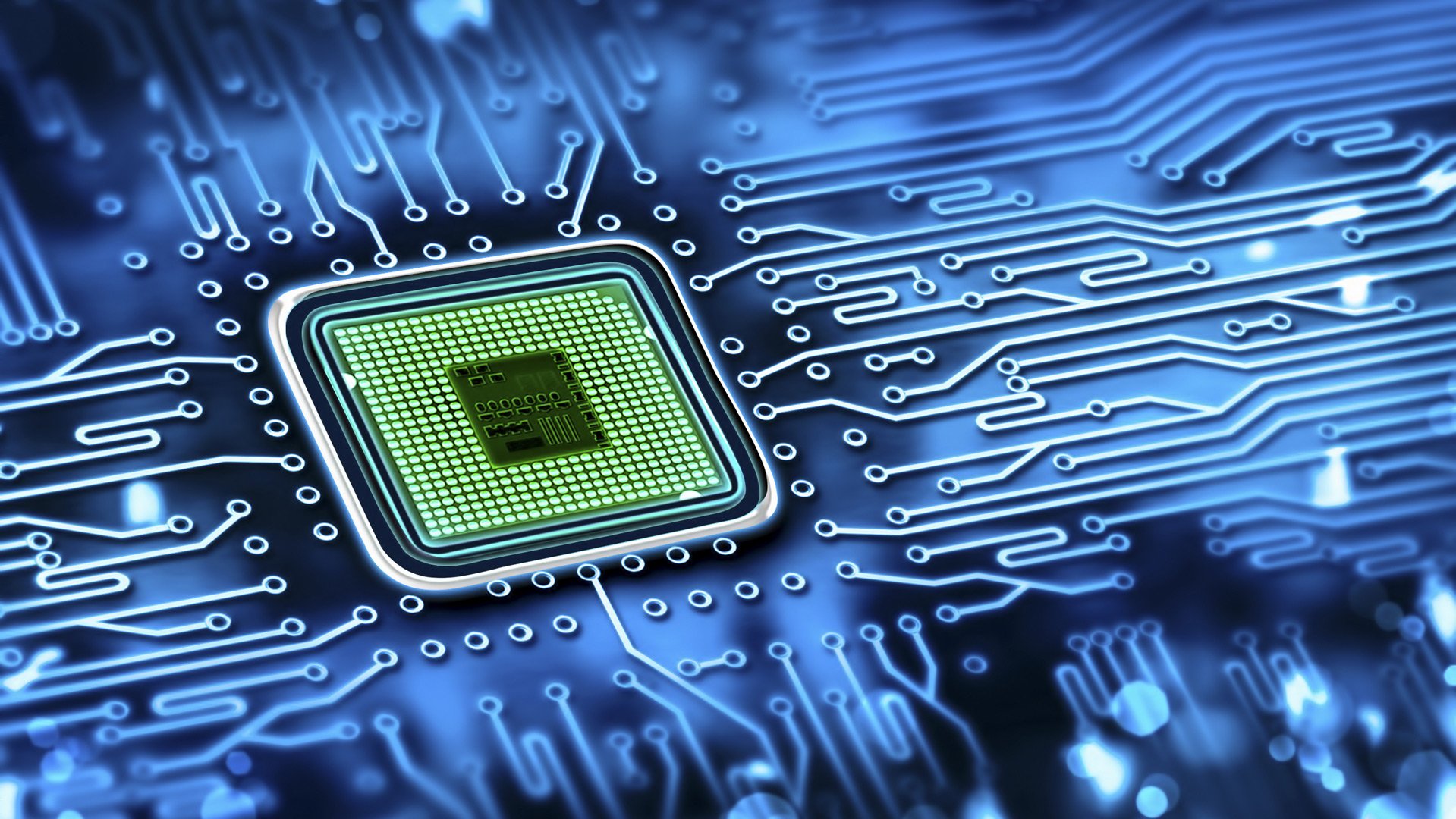
The Tg point, in the electronics assembly / soldering industry, represent the world’s worst ever practice approach. Nobody, but nobody, pay attention to some scientific, technological point of views. All “well-known, professionals, Chinese” manufacturers – money hungry persons / policies, let outside the most important points that MUST be respected. It is incredible how we, the clients that buy that errors / worst practice / scrap percentage lost and so on, it is incredible that we… (like an energumens penguins), only applaud, like, share, celebrate all that aberrations on LinkedIn, Tweeter, Facebook and so on.
Tg point - we need to stop, only for a moment, and think. Thinking doesn't heart. We need to use best, not worst, practice.
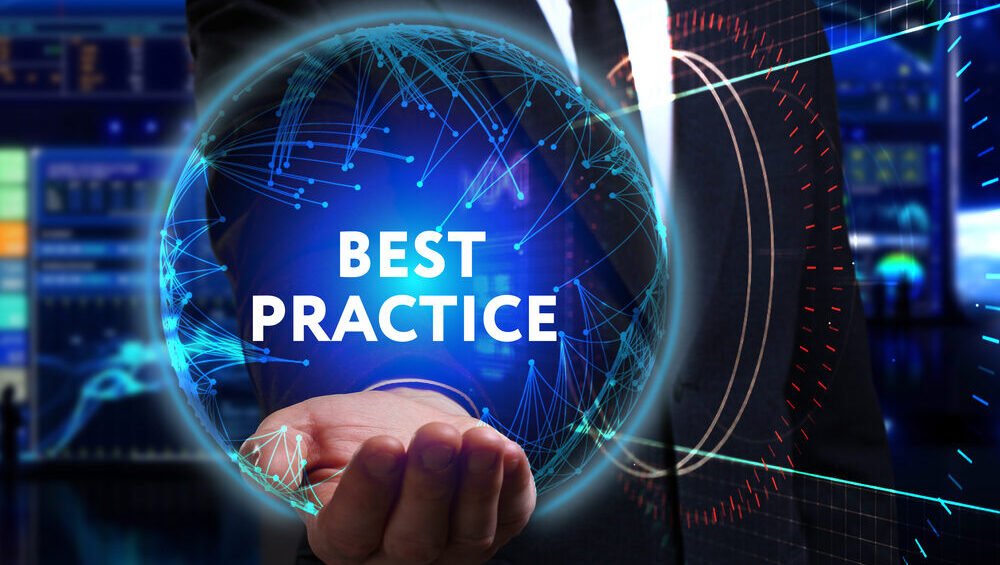
An entire industry forgot about Tg point, CTE, accuracy, best practice and so on...
When we’ll speak about Reflow process, Rework process, BGA Rework Stations, Reflow ovens and so on… the great forgotten is the Tg point (are more… like CTE and so on…). In the reflow process, when the assembly of electronics components on the PCB, are made for the first time, the Tg point can’t be respected. That is the nature of the first Reflow process. In the first Reflow process, all world of electronic assembly make the same errors, have same worst practice ever approach about Tg point.
Due to the obsolete technology that they’re using, engineers incompetence, money hungry policy / people, all “well-known, professional manufacturers”, on the initial first Reflow process, heat the PCB at 250 °C.
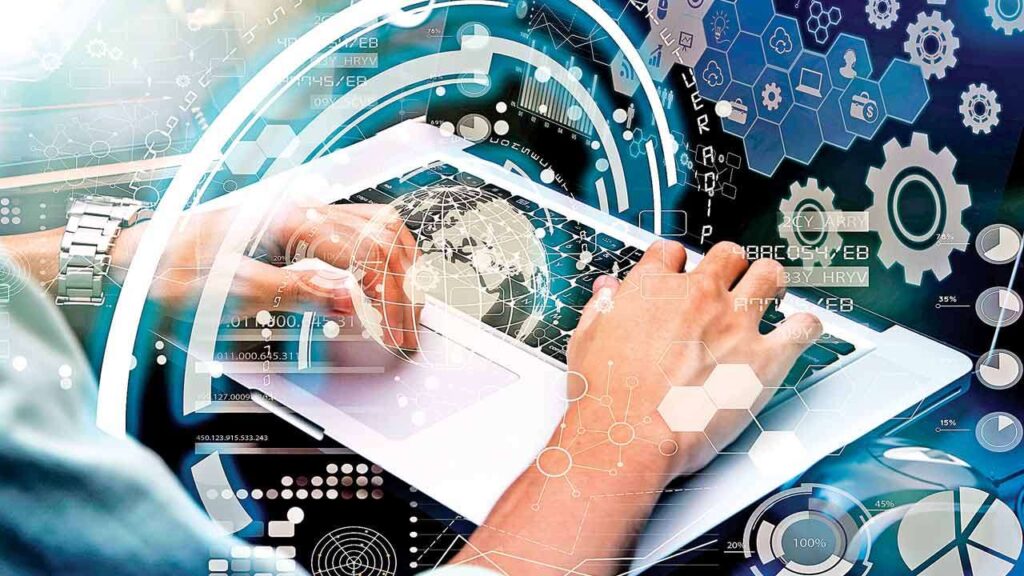
Science, technology, best practice Vs pseudo-science, pseudo-technology, worst practice.
They don’t pay attention to the psychical proprieties of the PCB. I can’t believe that the human evolution achieve this point without knowledge of the basics, the basics in soldering. Imagine where the humans can be, if all we are respect the science, technologies. Speaking about Reflow process, the entire electronics assembly part of the humanity, use the world’s worst ever practice approaches.
Use Reflow ovens, use vapor phase reflow process, use some aberrant soldering techniques that were used from year 1960. That money hungry policy have a huge amount of scrap board on the assembly process chain. Here you can read about the best practice ever approach on Tg point. Click or touch or use the menu to go.
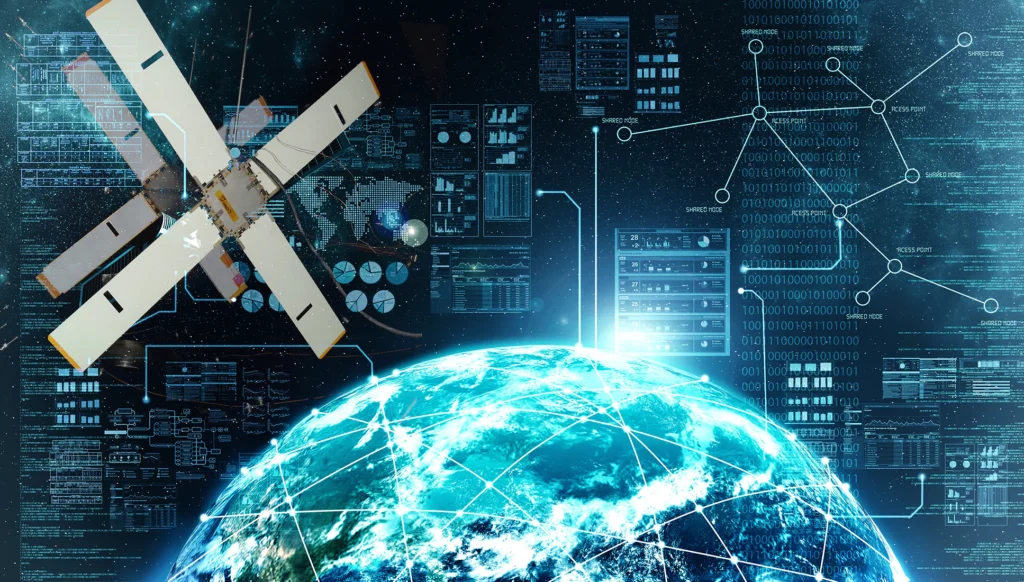
Add Your Heading Text Here
A typical / traditional reflow process time (from when the PCB enter, in the reflow oven until is out from reflow oven…) are about 3 to 5 minute. The same typical / traditional reflow process spend about 150,000 W/h (150 KW/h) to heat 3 meters to 5 meters of boards. What if I’ll tell you that I have a revolutionary technology / selective that respect the Tg point from start, from the first component’s assembly point, same job are does in 10 to 15 seconds with 1000 W/h (1 KW/h) of consumed power?!
And the entire board are heated under 80 °C?! But, that is science, is technology, that is best practice. I’ll present that on another website of my projects, BGA-Rework-Station.com. Click or touch or use the menu to go…
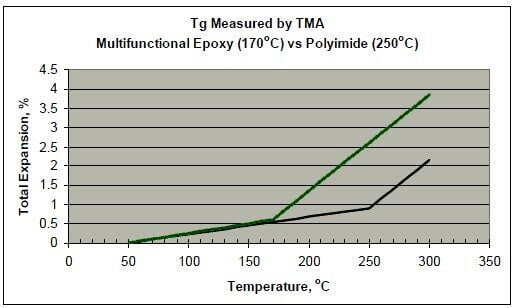
Let's speak about Tg point, it is important or not?! If it is important, why it is impostant.
In the above image, you have an example about the Tg point vs total expansion. The most important thing is the wide temperature difference on Tg point between different type of PCB’s, different materials, different thickness, different copper layer thickness and so on. In the above image are only difference between two materials, but in the market are a huge amount of materials with the Tg point from 110 °C to 280 °C. In almost all cases, we don’t know the type of material / PCB. When that fact appears, that is the worst ever practice / approach to heat the PCB / board over the Tg point.
As I’ll say on another post, the Tg point is the point where the PCB change his state from glassy like state to rubber like state. As you see in the above image, the total expansion is bigger when the PCB is in the rubbery state. The total expansion is important on that state (grow up from 1% to about 3.5%). So… here we underline two words… Thermal stress.
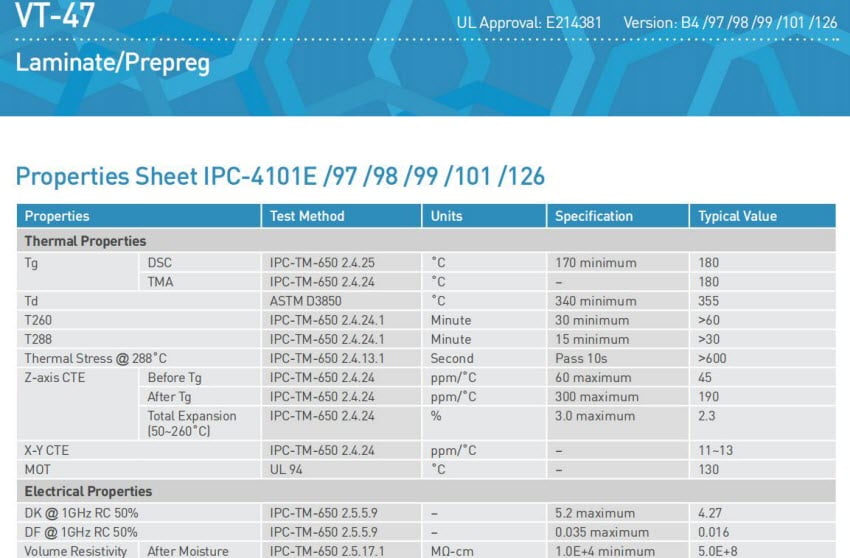
Let's speak about CTE, it is important or not?! If it is important, why is important?!
CTE is the PCB expansion on transversal plane (Z axis). As you can see on the above image, the CTE have two expression values. The first value is CTE below Tg point, the second value is CTE above Tg point. On that case, CTE < Tg = 45 ppm, CTE > Tg = 190 ppm. As you see, the value of the CTE is 4.22 grater when the PCB material is above Tg point. Here we underline two words… Thermal stress.
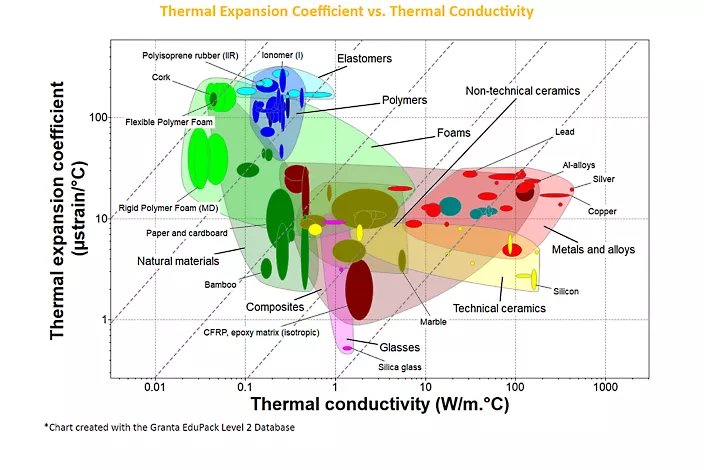
Let speak about copper thermal expansion, it is important or not?! If it is important, why?!
As you’ll see in the above image, not exist two materials with the same thermal expansion value. On a PCB, we speak about two materials thermal expansion factor, copper and fiber-glass + epoxy resin. I can assure you (I don’t search at this moment a graph) that the thermal expansion coefficient is 10 time less than the fiber-glass + epoxy resin. What that mean?!
That mean that at this difference the copper dilate and contract with different dimensional constant that fiber-glass + epoxy resin. That mean a huge mechanical stress on the bond between that two materials. When appear that mechanical stress?! When we apply heat on that system, when we are heating the PCB. More heating temperature = more mechanical stress. Here we underline… Thermal stress.
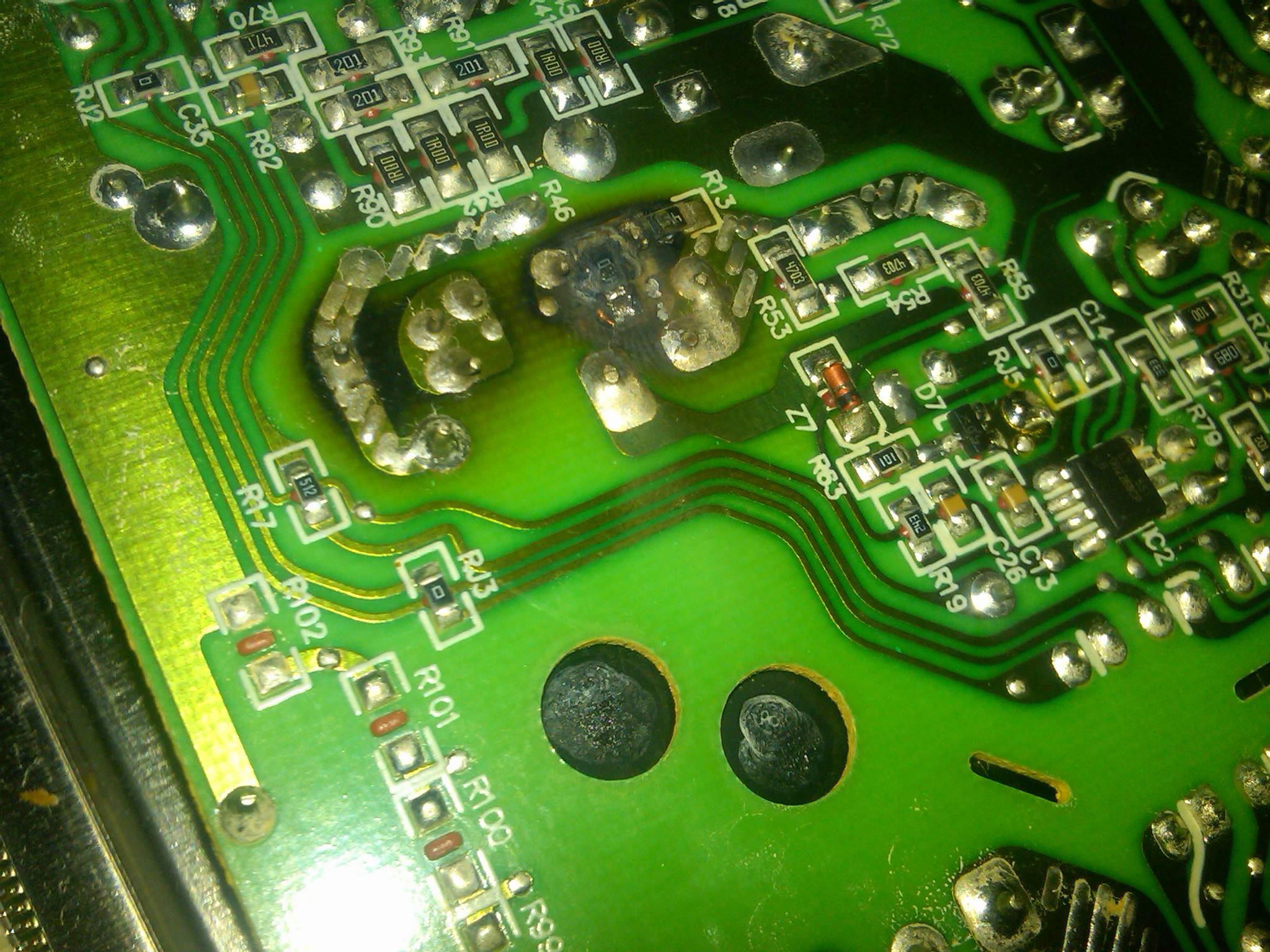
Let's speak about insulated layer of PCB, resin / glass-fiber composite, it is important?!
The function of that “insulated layer” is what these therms say, insulator, electrical insulator. When uncontrolled heat is applied to a PCB, that PCB has the tendency to change his proprieties from electric insulator to electric conductor state. It changes the proprieties in a carbon like state. More heat = more stress. When “well-known, professional, Chinese” manufacturers, use hot air (at 380 °C – 400 °C), are very close to this point. Same behavior is happening when the same “well-known, professional, Chinese” manufacturers use uncontrollable “Black-IR” at highest temperature that hot air. Thermal stress.
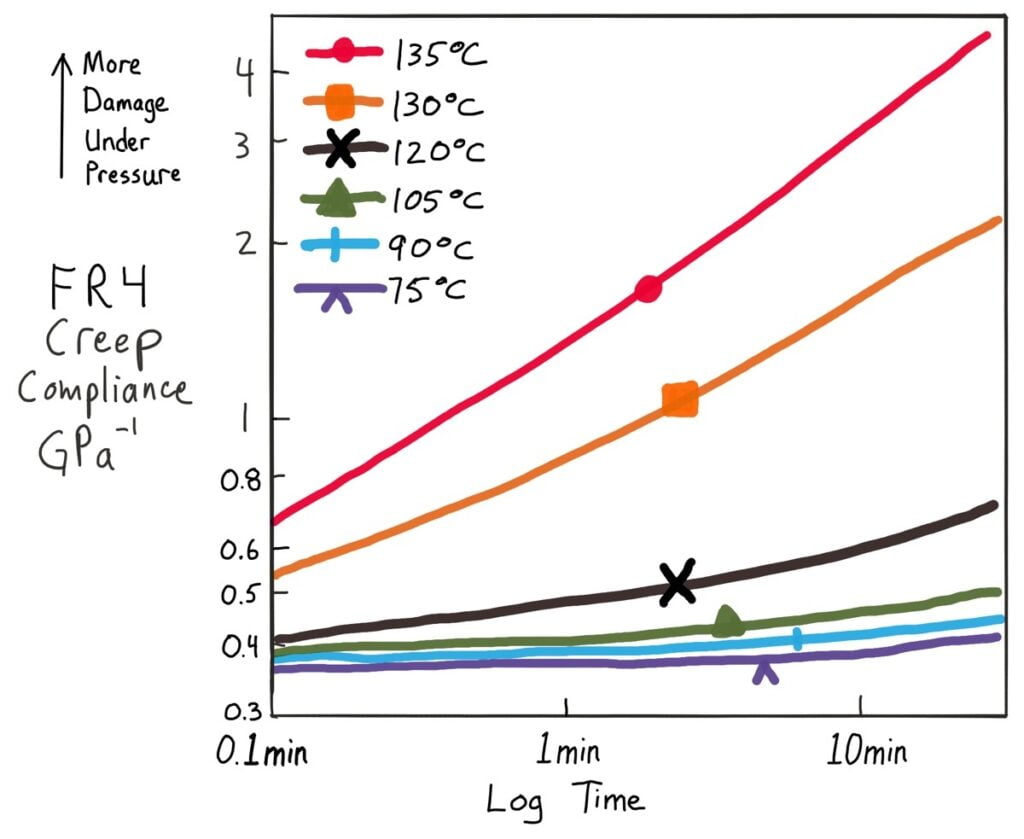
Let speak about PCB thermal stress, it is important or not?! If it is important, why?!
As you see in the above image, more temperature + more time = more thermal stress. When we heat the board or overheat them (when we heat the board above Tg point), we apply an unnecessary thermal stress that generate a high risk to break something. So simple… Again, we can underline that two words… Thermal stress.
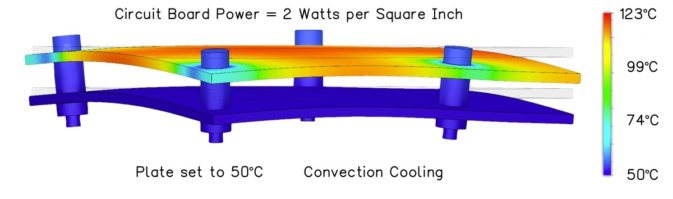
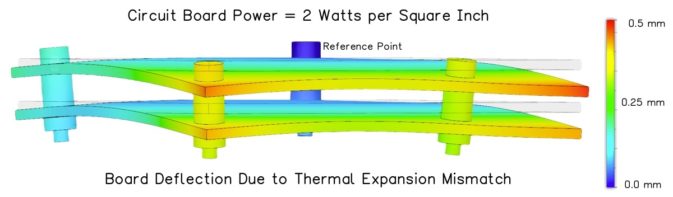
Let speak about bending due all stress, it is important or not?! If it is important, why?!
A PCB, at room temperature, normally is plane. When we heat it due to different materials stress behavior, the PCB will bend. In that case are impossible to solder with high quality a BGA for example on a round surface. Thermal stress.
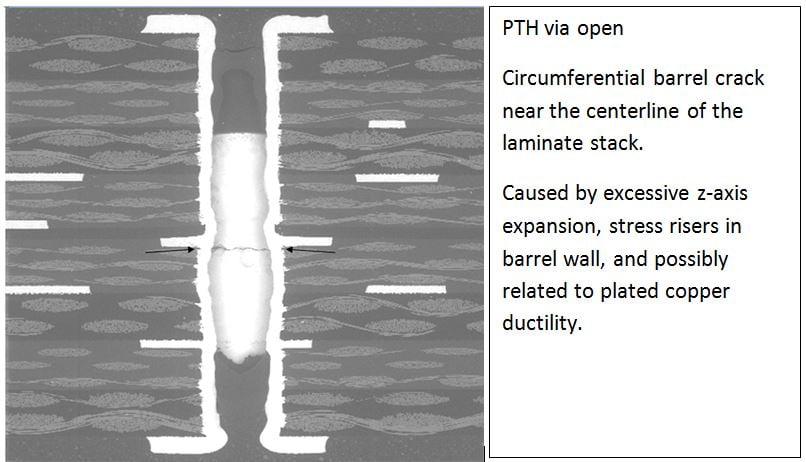
Let speak about vias thermal stress, it is important or not?! If it is important, why?!
The vias, it is not important that the vias is true holes or not, the vias are made from electrolytic copper. That type of copper is very brittle. If we heat the PCB, the board will expand, when the board expands, when a board expands the risk to one or more vias breaks are huge. Thermal stress.
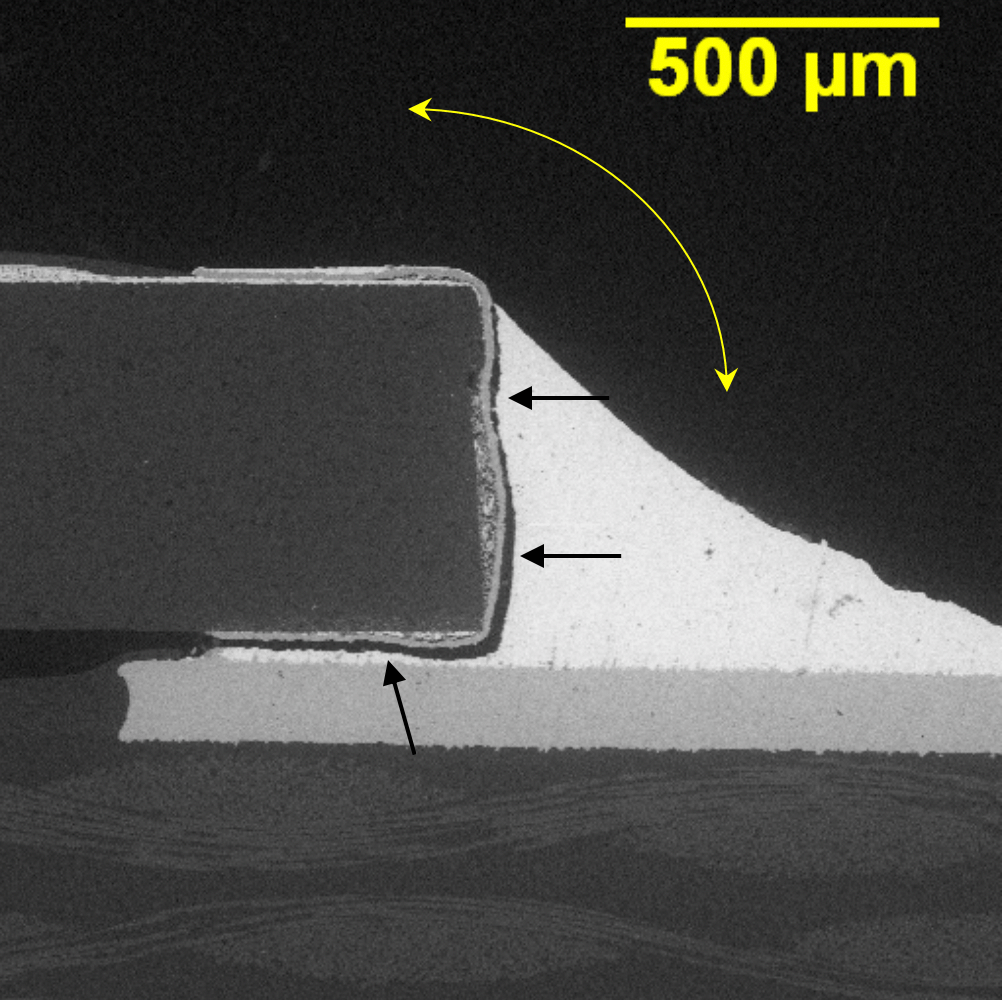
Let speak about components stress, it is important or not?! If it is important, why?!
When “well-known, professional, Chinese” manufacturers, heat the entire PCB at 200 °C – 250 °C, on a rework process for example, they put in risk / danger all components from that PCB / board. If a crack is started before, with that worst ever approach, the crack will be ended to produce. Thermal stress.
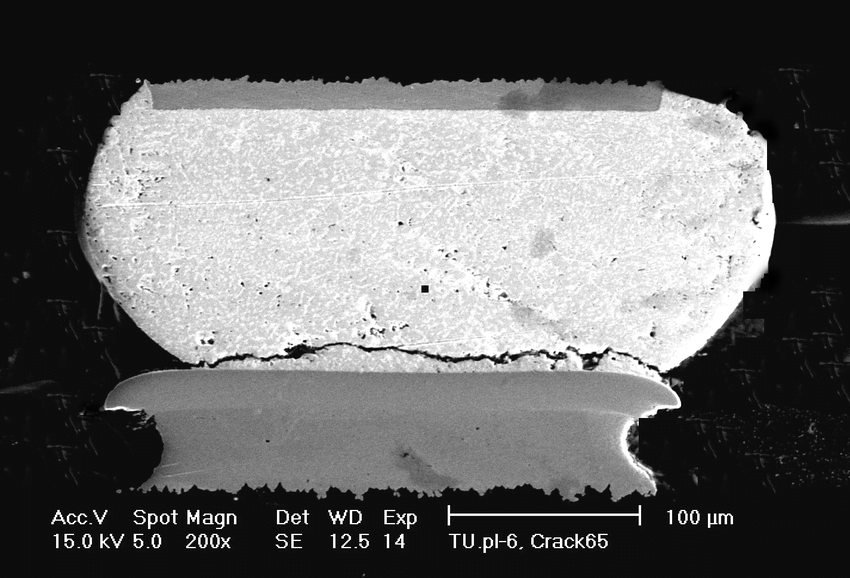
Let speak about BGA balls thermal stress, it is important or not?! If it is important, why?!
Same as above, when “well-known, professional, Chinese” manufacturers heat the PCB / board at 200 °C – 250 °C, even the balls from a BGA that are not worked will crack. Thermal stress.
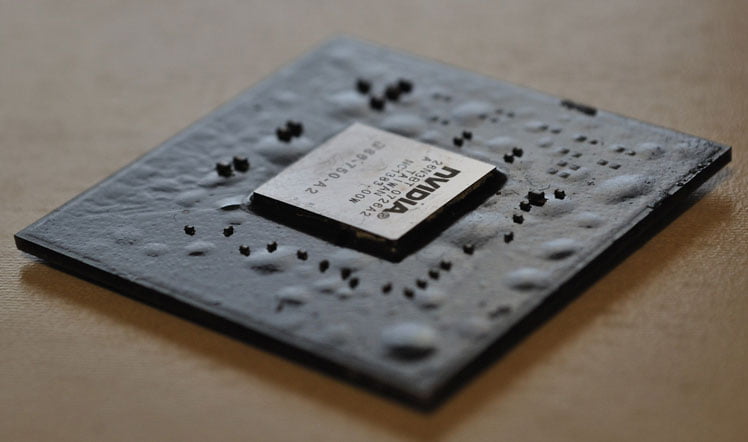
Let speak about components / BGA stress, it is important or not?! If it is important, why?!
With the pizza machines, popcorn machines, Santa Claus cousin that “well-known, professional, Chinese” manufacturers heat at 200 °C – 250 °C the PCB / board / BGA / components with hot air / hot gas at 350 °C – 400 °C or with “black-IR” at highest temperature than that, the only result can be… a popcorn BGA / PCB. Thermal stress.
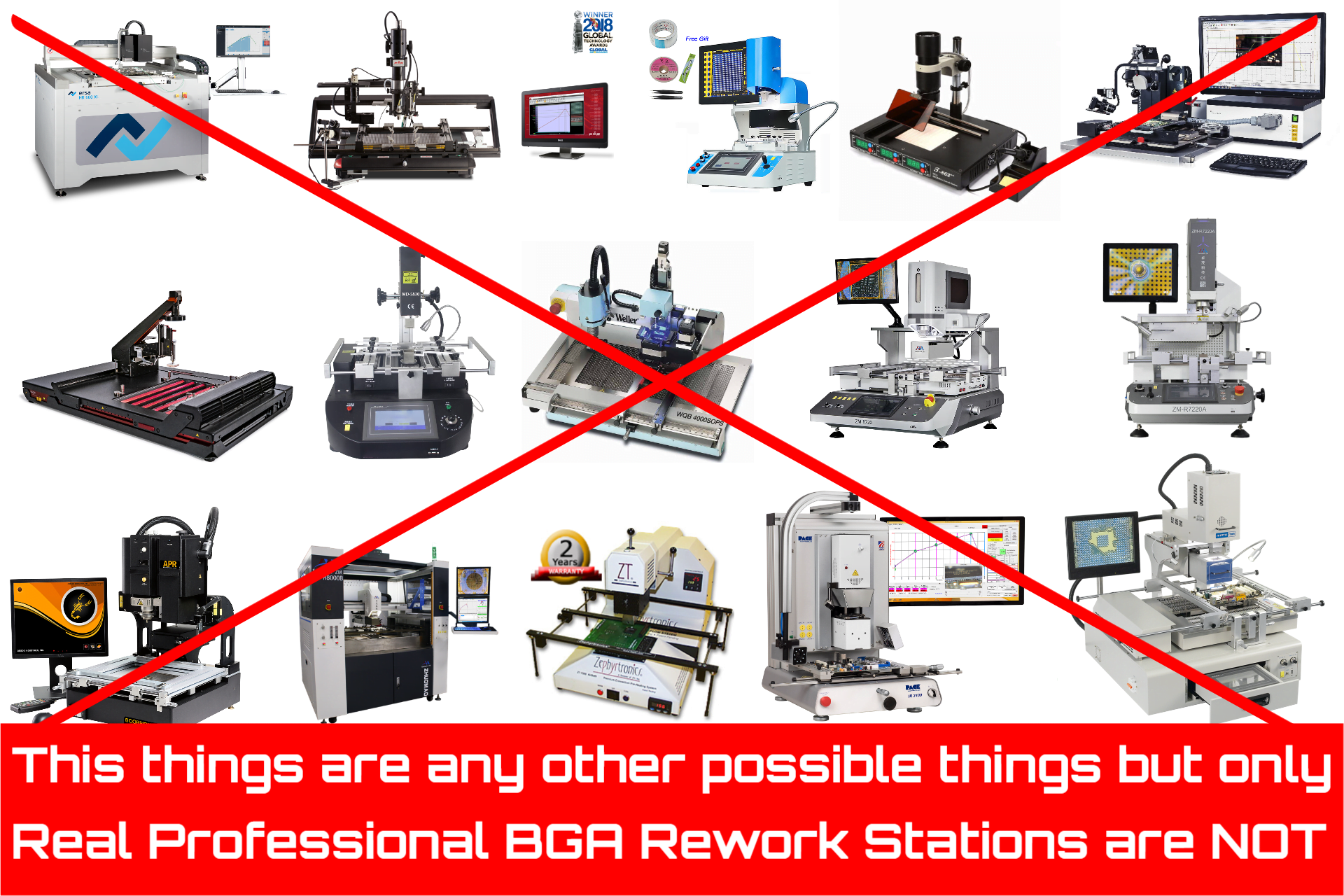
"Well-known, professional, Chinese" manufacturers garbage's that all they sell you with lies, cheating's...
As your easy can see, the common two words are “Thermal stress“. That words generate the worst defects / problems in electronics. These words MUST be avoided. The “Thermal stress” MUST be avoided. That two worst ever, are generated by the world’s worst ever practice approaches, heating the PCB / board at 200 °C – 250 °C, that “well-known, professional, Chinese” manufacturers, use on his pizza machines, popcorn machines, Santa Claus cousin that they sell to us as “professional BGA Rework Stations“.
For us, the real professional electronics guys, are very important a step-by-step approach when we want to buy a real professional BGA Rework Station. It is important that before spend money, be informed. It is important to have the mandatory knowledge, not be ignorant. Furthermore, it is important to be documented, it is important to have a solid base to choose what is the best for us, not what some amputated brain manufacturers try to manipulate us.
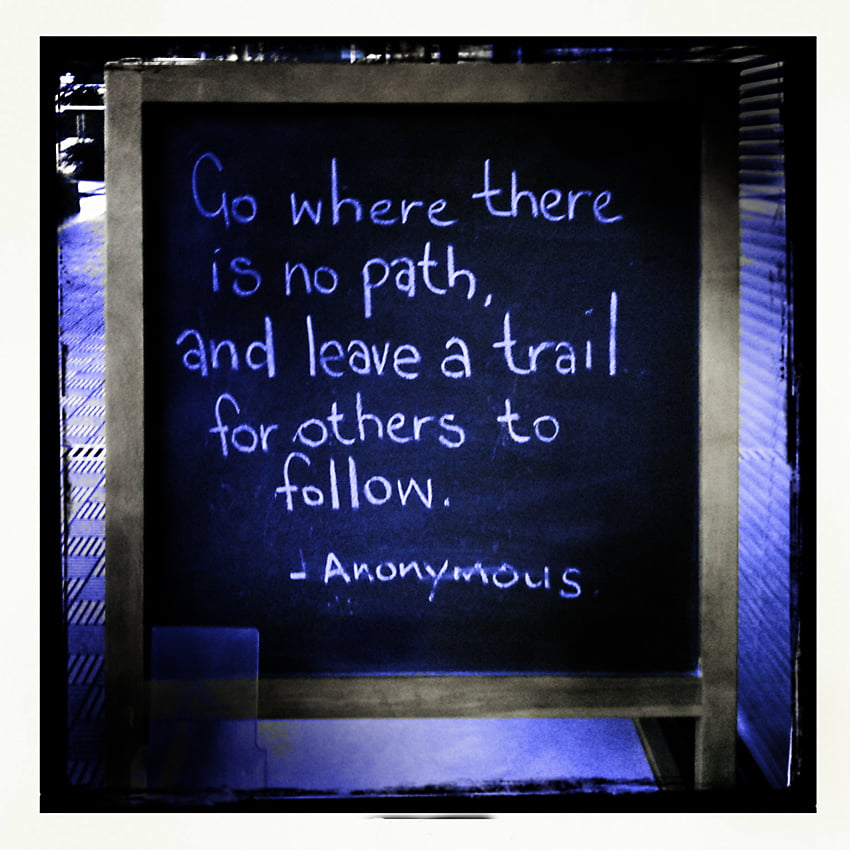
I'll choose to NOT buy all garbage's from "well-known, professional, Chinese" manufacturers.
In 2012, with more than 10 years ago, when for the first time I’ll want to buy a real Professional BGA Rework Station, that information (that information that you can read on this website BGA-Rework-Stations.com and on the BGA-Rework-Station.com) doesn’t exist. I’ll was obliged to read and select the utile / concrete / true / scientific / technological / best practice from an infinite unuseful information that are on the internet. I need to compare all the world’s worst practice approaches from the internet that “well-known, professional, Chinese” manufacturers, use on his pizza machines, popcorn machines, Santa Claus cousin.
That they sell to us as “professional BGA Rework Stations“, with the best practices, with science, with technology. In fact, touch me, a huge and hard work that takes me on unexplored ways from this beautiful sciences, the electronic sciences. It was a long, long journey that now, when I’ll write that rows, are close to the finish line. The only question that remain, is that exist another persons that think like I think!!!
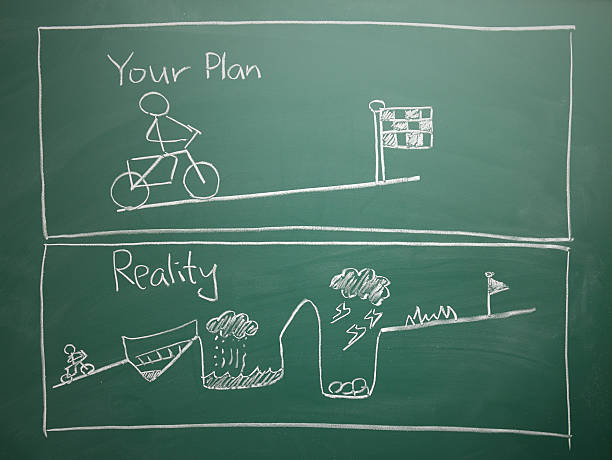
As all in this life that have value... A long and unexpected journey, some more steps until the finish line.
For me, with ten years ago, was a long and complicated journey to save my money and my time to be worst ever spent. At that time doesn’t exist even one real, true, clear information about that all “well-known, professional, Chinese” manufacturers, use on his pizza machines, popcorn machines, Santa Claus cousin that they sell to us as “professional BGA Rework Stations“. I was tempted to choose the easy way, I was tempted to be superficial, ignorant and buy what at that moment seems to be the “right choice“. Only my intuition, my reverse engineering skills save me to throw to the trash more than $60,000. But I was a lucky guy that I’ll stop and think, before spend money. More than 100,000 persons (in my opinion) don’t stop before make an inversion. Nowadays, much of them are crying all over the internet.

You have the luck to go on an already made path. Try to use the information already made.
In the present, for you is far simple to choose a real Professional BGA Rework Station. First you look on the internet. If you have the chance to discover the BGA-Rework-Station.com and BGA-Rework-Stations.com… You have luck. Read with attention all information on that two websites. After that, you must take a look at “well-known, professional, Chinese” manufacturers, use on his pizza machines, popcorn machines, Santa Claus cousin that they sell to us as “professional BGA Rework Stations“. If something from that convince you… Buy it. If so… you will cry after. And the money… Are blowing in the wind. Be a part of that more than 100,000 persons that buy with ignorance. But… don’t cry after…
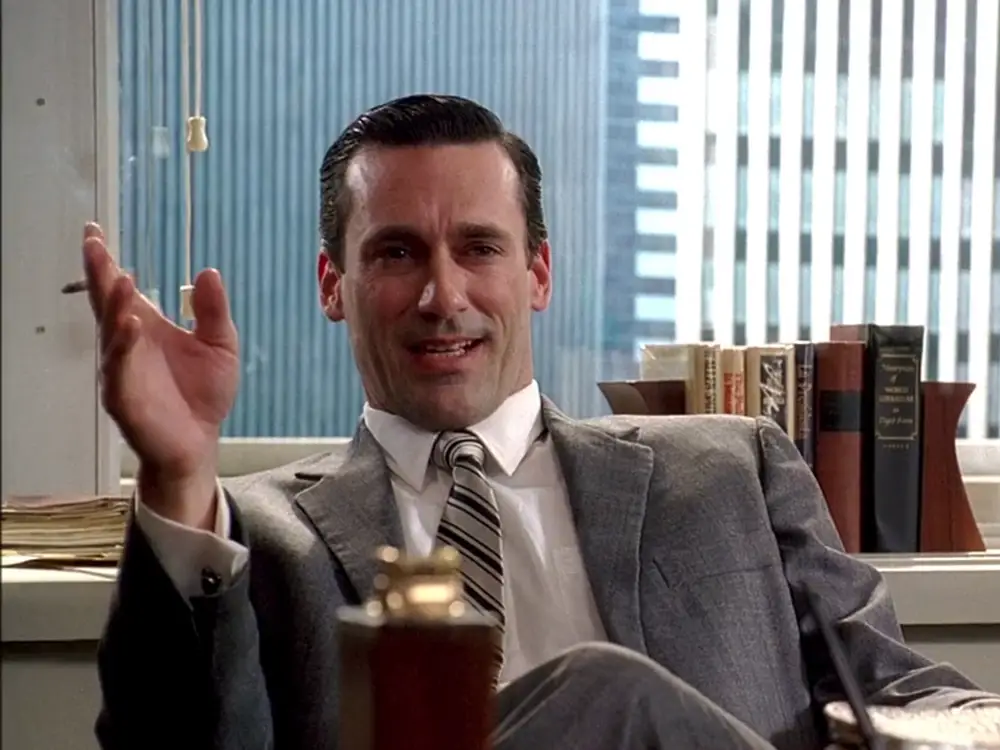
What if the "well-known, professional, Chinese" manufacturers not convince you to buy some garbage?!
What if “well-known, professional, Chinese” manufacturers, use on his pizza machines, popcorn machines, Santa Claus cousin that they sell to us as “professional BGA Rework Stations” not convince you, after that you’ll read all the information on that two websites?! Well, here is not a simple answer. I can tell you what I do when all them doesn’t convince me to buy something from their garbage’s. I’ll start my own researches and developments to build a real Professional BGA Rework Station. You can do the same, you can start your own researches and developments to build your own real Professional BGA Rework Station.
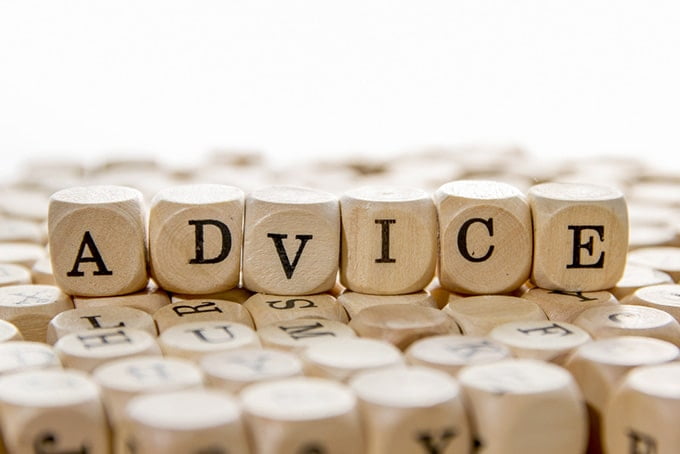
You have the luck to go on an already made path. Try to use the information already made.
If so, I can tell you that with some years (many) or with a complete team of engineers you can achieve this. In this life, almost all it is possible. Among that, you’ll need about $500,000, yep… About half million dollars to invest in your years of researches and developments process. You (or your engineer’s team) MUST know / learn about psychics, optics, chemistry, materials technologies, mathematics, mechanics, tools, resins, ceramics, finishing, electronics, hardware, software, management, marketing, social networking, banks, investors and much more.
I E S N L.L.C. - Proudly to be an American company - Since 2012 we build the future.
All that took me more than 10 years and about $500,000 that I’ll spend over that ten years. If that is ok for you… Go for it. If that is not ok for you… And wont to buy an already manufactured real Professional BGA Rework Station… Pay attention to these two websites, the BGA-Rework-Station.com that website, and BGA-Rework-Stations.com… Soon will appear another new website, i-esn.com. On this website you can buy world’s first and probably the only one real Professional BGA Rework Station. Among that, they are manufacturing products that respect the world’s best practice approaches in electronic sciences, they will have some interesting purposes for you.