BGA Rework Station - BGA / Chip - top-heater - Direct Energy Transfer - DET® - probably the best practice ever approach.
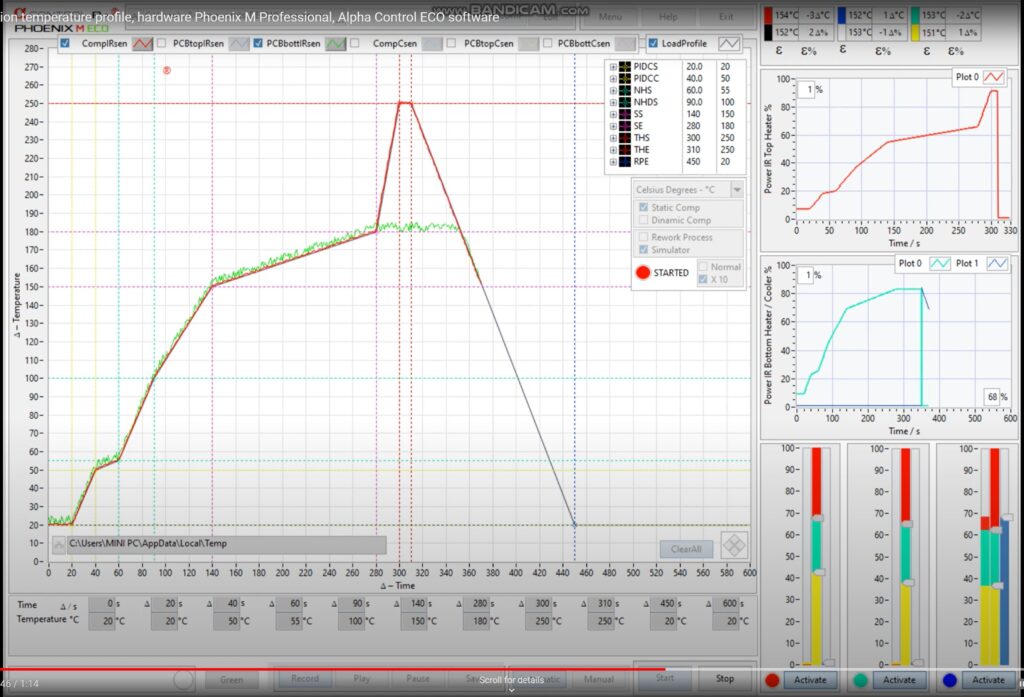
An almost perfect BGA Rework Process - software - Alpha control - ECO version, ± 1 °C - Top-Heater, ± 2 °C - Bottom-Heater.
Above image are from early tests (early alpha versions in 2018 – if I’ll remember correctly), when I’ll start the tests for best practice approach for Real Professional BGA Rework Process with a Real BGA Rework Station. On this case (from above image) I let with intention the ± 1 °C – Top-Heater temperature errors and ± 2 °C – Bottom-Heater temperature errors, with the only purpose to visually see life on screen, if that measure order can be seen on screen. In the reality, I can obtain ± 0.5 °C – 1 °C of accuracy error (NIST traceable certificate – to calibrate the non-contact / contact sensors, I’ll use a NIST traceable certificate, temperature measurement system).
We must learn from the paste errors that the “well-known, professionals, Chinese” manufacturers make from 35+ years, where so many possibilities were ignored and invent the future, a future where the science, technology, best practice, sustainability make the rules. From here come the motto – “When the future doesn’t exist, I’ll invent it“. You are welcomed to this future, and believe me that all your help are in invaluable contribution to put in value the bet practice approach in electronics sciences. Complete detail about my projects here… BGA-Reworl-Station.com (click or touch to go to that – another website).
For a real Professional BGA Rework Station, for a real Professional Rework Process, in fact, we need three simple things, we need three MUST-have. First – the right energy part of electromagnetic spectrum, second – high accuracy for temperature reading, third – high accuracy temperature control. Below let spread some details, for patents pending questions, I’ll can’t describe in detail all aspect above how can be made that, but… to achieve 100% yield – 100% repetitively rate, all details that you read on this webpages are a MUST / a must-have best practice approaches. Of course, here you can read about the worst practice ever approach.
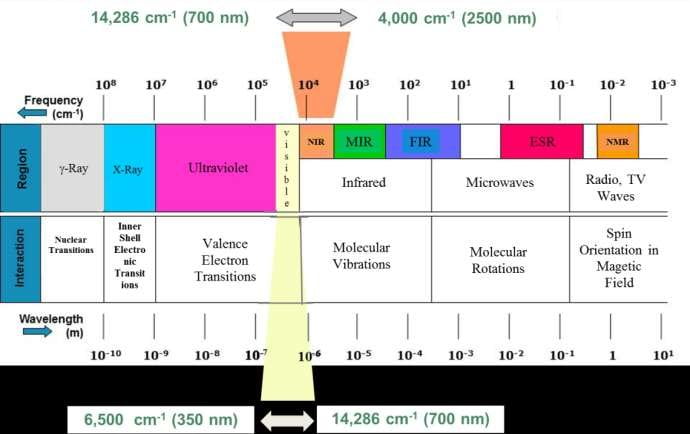
The right part of the energy spectrum - the correct choice.
Unlike the “well-known, professional, Chinese” manufacturers that use the worst ever practice approach, the direct convection method (huge inertia, poor temperature medium thermal power, high difference between the energy generator / BGA / PCB temperature, almost impossible control of the Rework process), if we choose the right method to transfer the energy from energy generator / emitter to BGA / PCB ve have the success guarantied. That manner – direct energy transfer approach not only that give us to generate – transfer the energy to the BGA / PCB without any risk for them but, are completely unharmful part of electromagnetic energy / it is not dangerous, completely safety to operate.
As a conclusion, a must-do-not use – direct conversion and a must to use Direct Energy Transfer – DET® – 100% yield.
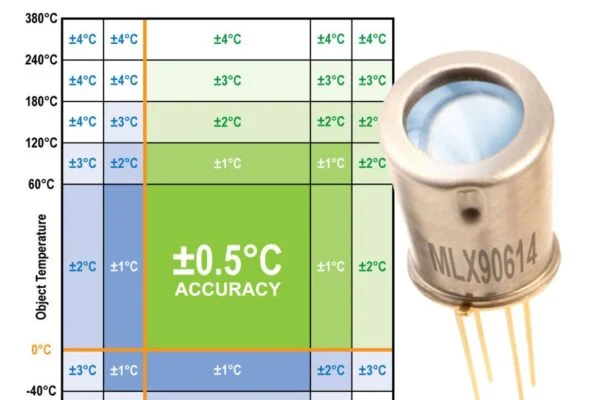
The right approach to read the temperatures with high accuracies.
Unlike the “well-known, professional, Chinese” manufacturers that use the worst ever practice approach, K-type thermocouple and non-calibrated non-contact-IR sensors, the best ever practice approach are dual. On one side, we need a contact sensor (a real contact sensor with his temperature transfer medium) and on another side, we need a high accuracy non-contact-IR sensors. The policy here is that one sensor type, dynamically calibrate another sensor type. In that manner, the accuracy that can be touch, are less than ± 0.5 °C.
As another conclusion, a must-do-not use – K-Type thermocouples or non-calibrated non-contact-IR sensors and a must to use – high accuracy – NIST traceable contact temperature sensors (among contact temperature transfer paste) combined in same time with non-contact-IR sensors to do the Dynamic Compensation®.
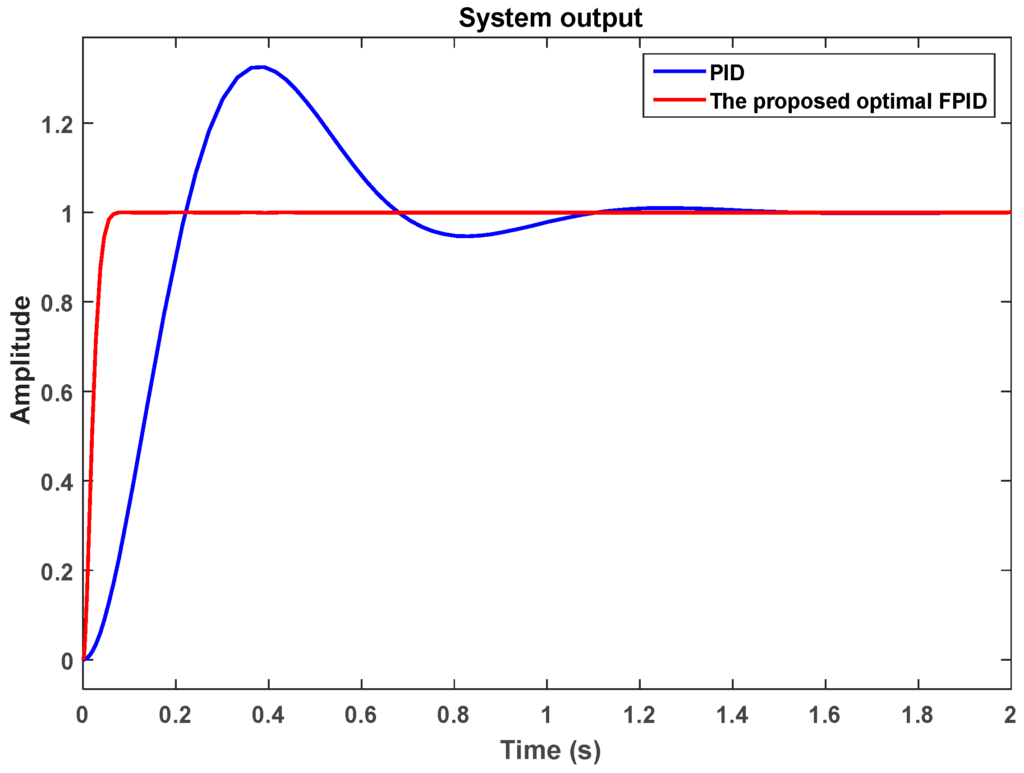
The right approach to high speed / high accuracies' temperature control.
Unlike the “well-known, professional, Chinese” manufacturers that use / try the worst ever practice approaches to control the temperature (in fact an impossible temperature control due to his convection method approach). Here we use a near perfect controllable approach (Direct Energy Transfer – DET®) that do NOT transport heat / temperature, it transports adequate spectrum part of electromagnetic energy. That electromagnetic energy transferred to PCB / BGA produce the phenomena named “self-heating”. In that manner, we can obtain the lowest possible inertia (almost zero inertia), ultra-high speed near to perfect control…
The using of DET® among with AI assisted – Fuzzy Logic PID Control® mean probably the best ever practice approach for a Real Professional BGA Rework Station and 100% yield.
You can see above, we have three new invention (patent pending) and three terms - registered trademark pending, apported to a Real Professional BGA Rework Station - Direct Energy Transfer - DET® / AI assisted - Fuzzy Logic PID Control® / Dynamic Compensation®. It's only the starting point of my journey, "Go where there is no path, and leave a trail for others to follow".
Below I’ll try to exemplify what mean best ever practice for top-heater, the most important part of a Real professional BGA Rework Station. I’ll make this with the limitations of patents / trademarks pending conditions, so the information is not complete. I’m very sorry about that, but if nobody among of 35+ years can’t think in a scientific / best practice point of view, not deserve to have for nothing all solution to his problems. So… “Well-known, professional, Chinese” manufacturers, you can pay attention to these things… You don’t have the intellectual mandatory intelligence coefficient to copy… something.
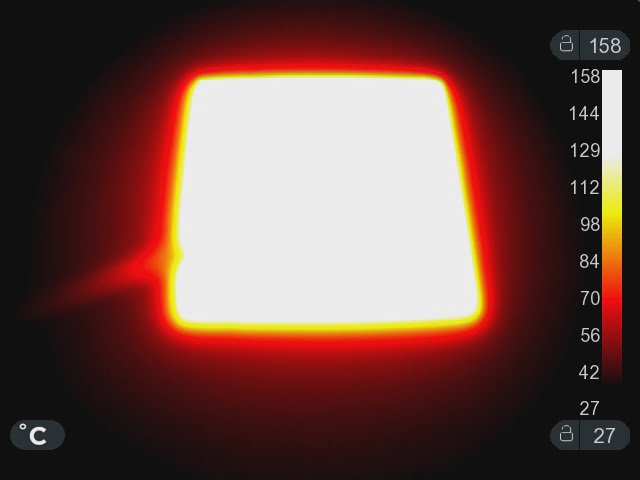
Direct Energy Transfer DET® generator - Top-Heater.
- Power – I test the powers from 150W to 1000W consumed power.
- Direct Energy Transfer generator DET®.
- Electromagnetic energy spectrum – somewhere in the IR part.
- Perfect Shape® – shaping the emitted electromagnetic energy in square / rectangular / round (for LED’s, round connectors… etc.) shapes.
- Perfect Diffused® – Perfect spreading uniformity over entire BGA / chip array of electromagnetic energy emitted.
- Laser Like® – a laser like system approach for the electromagnetic energy emitter.
- Absolute Wide Control® from 5 mm to 55 mm, continuous variable square / rectangle, circular – dimensions.
- Manual / Automatic beam shaping® -. Manual or automatic possibility to adjust the shaping of the electromagnetic energy emitter.
- Red Pattern® – Visible red shape that represent the real transferred electromagnetic energy shape on the BGA / chip.
- Perfect Cut® – World’s highest performance Long-Pass Filter that perfect cut on 635 nm – 645 nm, the harmful visible light.
- X – Mark® – An clearly visible X mark over the Red Pattern® – That clearly / visible indicate the perfect focus diffused pattern.
- Work-Light – assure the complete visible lighting directed to the BGA / chip to illuminate the work zone.
- Sensors / close real view process camera, close-view process infrared camera, supports.
- Cool Control® – high-end technology (active, perfect shaped copper foam system) for high performance heat evacuation.
- Gold Cheap Spare® – Custom Gold platted reflector for electromagnetic energy emitter that use cheapest spare parts.
- Closeup Process, visible – vision camera®.
- Closeup Process Infrared – vision camera®.
- Fair Price®
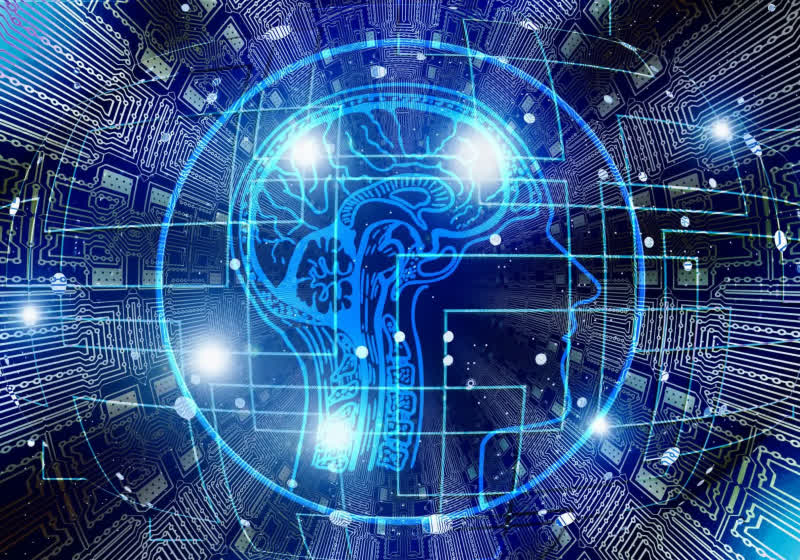
Inventions / innovations custom-made, special developed for the world's first Real Professional BGA Rework Station, code-name - Phoenix.
- Direct Energy Transfer – DET®
- Laser Like®
- Perfect Shape®
- Absolute Wide Control®
- Manual / Automatic beam shaping®
- AI assisted Fuzzy Logic PID Control®
- Dynamic Compensation®
- Perfect Diffused®
- Red Pattern®
- X Mark®
- Cool Control®
- Gold Cheap Spare®
- Closeup Process Visible – view Camera®.
- Closeup Process Infrared – view Camera®.
- Fair Price®
As you can easily see above, fourteen inventions / innovations, in-house, custom-made, to drive the world’s first real Professional BGA Rework Station. Nothing about pizza machine, popcorn machine, Santa Claus cousin device used for that purpose.
The world’s best practice approach technologies, the finest ever piece of sciences, many of them, NASA use in their space projects.
Pay attention please, above (on this page) are only Top-Heater part about… things!
With nowadays scientifically, technologically evolutions, I’ll clearly identify two perfect electromagnetic energy spectrum parts, perfect candidates that are the best choice, from practically point of view, to manufacture some real Professional BGA Rework Stations.
Here I’ll detail only the Infrared part of electromagnetic energy spectrum that is the cheapest approach from the two best practice approach possibilities.
We need to take in count the fact that the BGA / chips have a large dimensional variation (there exist BGA / chips from 1 mm square / rectangle to almost 80 mm square / rectangle). From the practical point of view, are impossible to cover with only one Top-heater version (dimensional power), the entire dimensional variation of the BGA / chips. From my researches result the fact that that entire dimensional variations can be covered with 3 top-heater variations (powers). Also, from my researches, result a simple correlation between the BGA / chip dimension and the top-heater consumed power. That will be based / expressed in W/cm2.
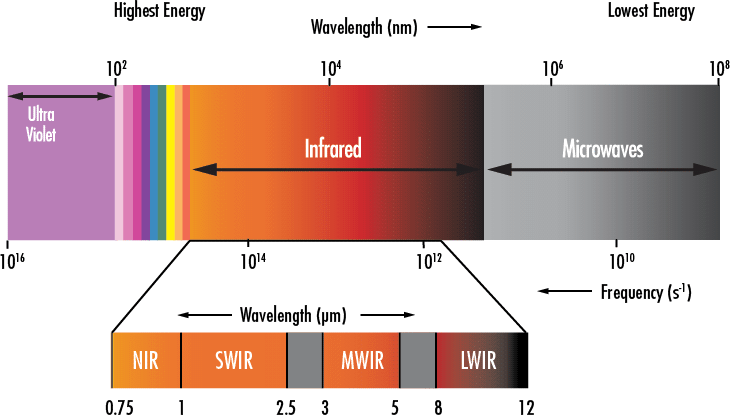
Direct Energy Transfer - DET®.
As I’ll say before, The right choice of the right part of electromagnetic energy part, are one of the most important best practice approach for a real Professional BGA Rework Station.
The Infrared part of electromagnetic energy are divided in some parts. NIR – SWIR – MWIR – LWIR.
The MWIR / LWIR is already used by “well-known, professional, Chinese” manufacturers among hot-air / hot nitrogen, and is already proved that all that are the worst ever practice approach (huge inertia, impossible to control and so on…) for a Real Professional BGA Rework Station.
So… Remain (due to the fact that “well-known, professional, Chinese” manufacturers can’t use the real science / technology)… So… remain… NIR – SWIR – The world’s best ever practice approach. But… Here come the minimum / maximum direct energy generator power to be chosen.
NIR - SWIR part of the electromagnetic energy spectrum + Correct minimum / maximum power choice are the best ever practice approach when we speak about Professional BGA Rework Stations.
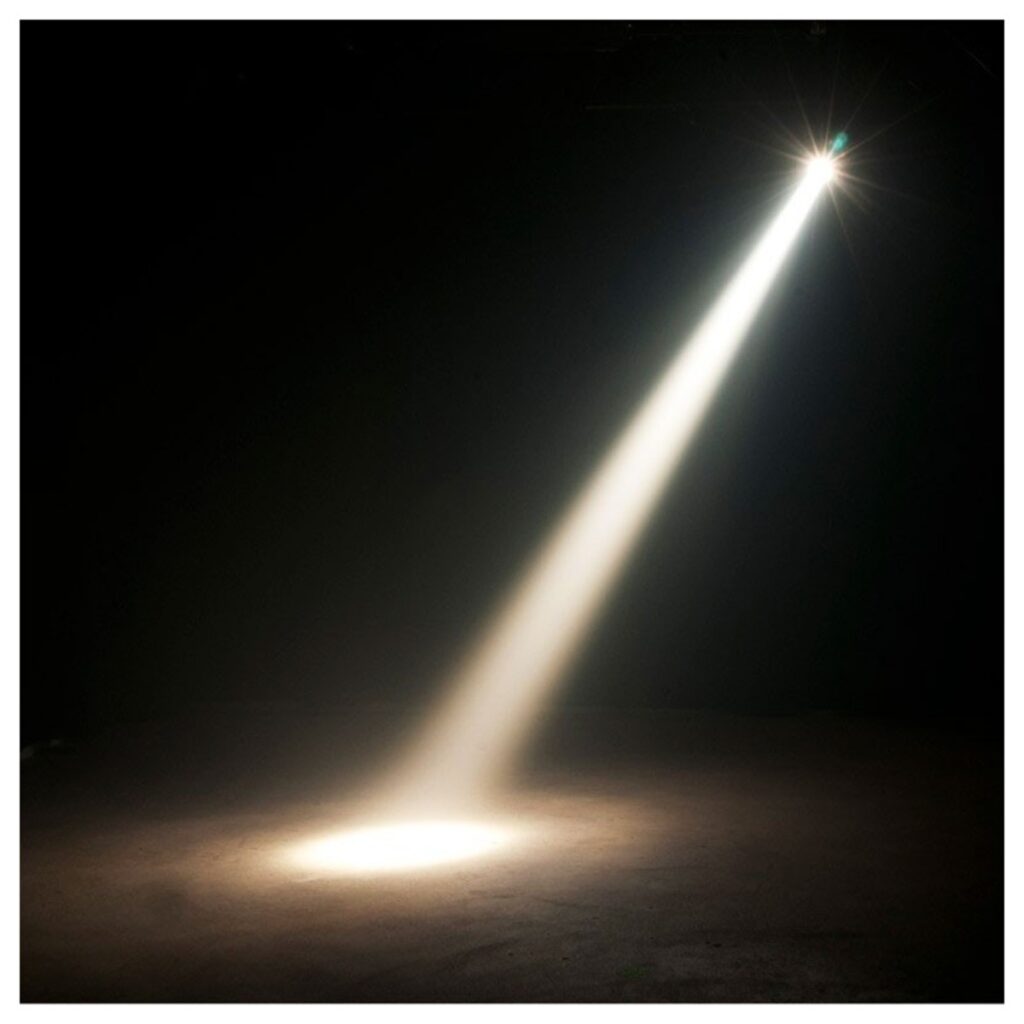
Laser Like®.
As the laser basics functionalities, the direct energy generator MUST respect some best practice approaches. The first and most important is achieving the maximum possible energy conversion efficiency (P-in / P-out). The power consumed to generate that energy reported to the power of energy resulted from the system.
As you clearly see on above image example with a light spot, exist two sides with light. One in the middle with high power, and around that another side with less power. In that case, only the highest part to be transferred to the target, remaining less power are useless and must be cut. If we cut inappropriately this energy we lose them, we lose about 30% – 40% of the electromagnetic energy generated.
Laser like® – system, intelligent cut that energy but do not waste them, it reflects that cut energy again on the primary reflector giving it infinite chance to be mixed with the already useful energy generated. In that manner, I’ll achieve more than 95% efficiency for produced energy from consumed energy (the 5% that are lost, are lost on the gold-plated reflectors assembly).
Laser Like® - Up to 95% electromagnetic energy conversion factor.
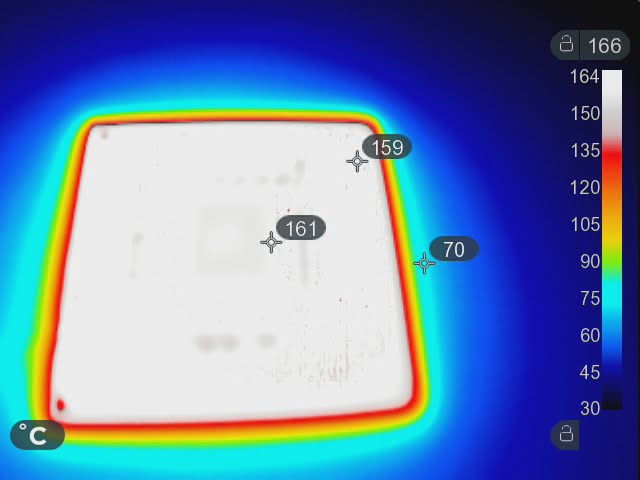
Perfect Shape®
Perfect Shape® – function is that to perfectly adapt the electromagnetic energy to only BGA / chip pattern / shape, avoiding irradiate with high power electromagnetic energy the adjacent (surrounding) heat sensitive components. As you see in the above image, at only 3 mm distance, the temperature difference is almost 90 °C. Thar mean a high step cutting of BGA / component temperature shape.
That approach respect the world’s highest best practice approaches practically possible.
Perfect Shape® - world's highest best practice approaches.
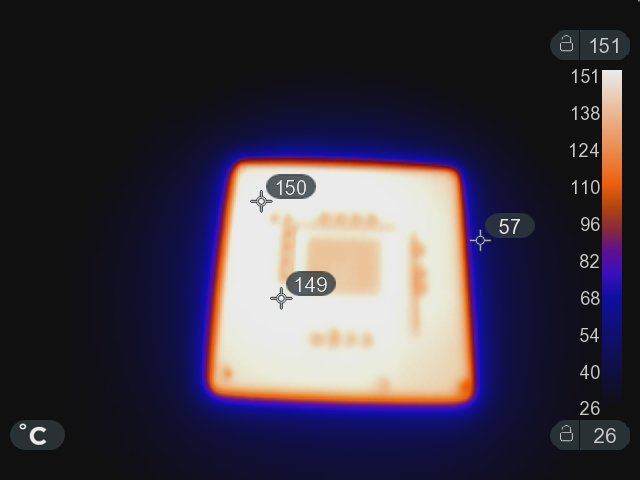
Absolute Wide Control®.
Absolute Wide Control® – assure the perfect uniformity of electromagnetic energy over the entire perimeter of the BGA / Chip and efficient cutting / reflecting the less uniform part, back to Principal reflector.
Their principal function is the adaptive shaping to wise identify and reflect the nonuniform electromagnetic energy applied to BGA / component.
An essential part of world’s best ever practice that MUST be respected.
Absolute Wide Control® - a must respect best practice approach.
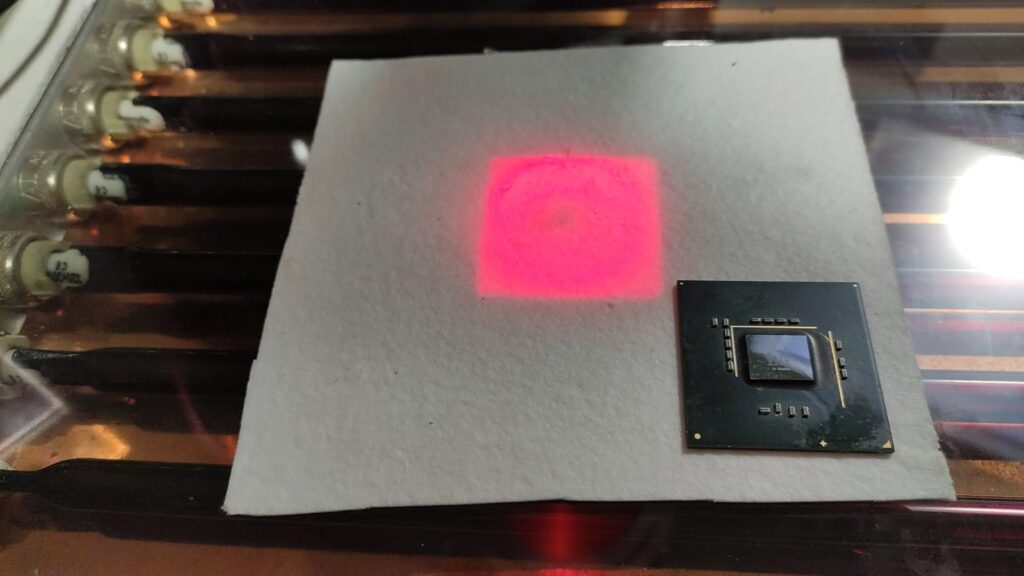
Manual / Automatic Beam Shaping®.
When a very complicated task (millions of shapes / dimensions / forms), become a simply / easy process.
When you’ll select the appropriate reference Rework Process (ex: N17E G1 A1), you’ll not only choose the right / predefined Rework Process parameters for that component reference, also, in same time, the system chooses for you the pre-programmed shape / dimension for that BGA /chip. The eventual needed corrections can be does in manual mode and lately stored as standard parameters.
Also, for a new component shape / dimension that at that time doesn’t exist in your / our database, you can easily establish the appropriate shape / dimensions, and lately you can store as default shape dimension for the electromagnetic energy spot.
Add Your Heading Text Here
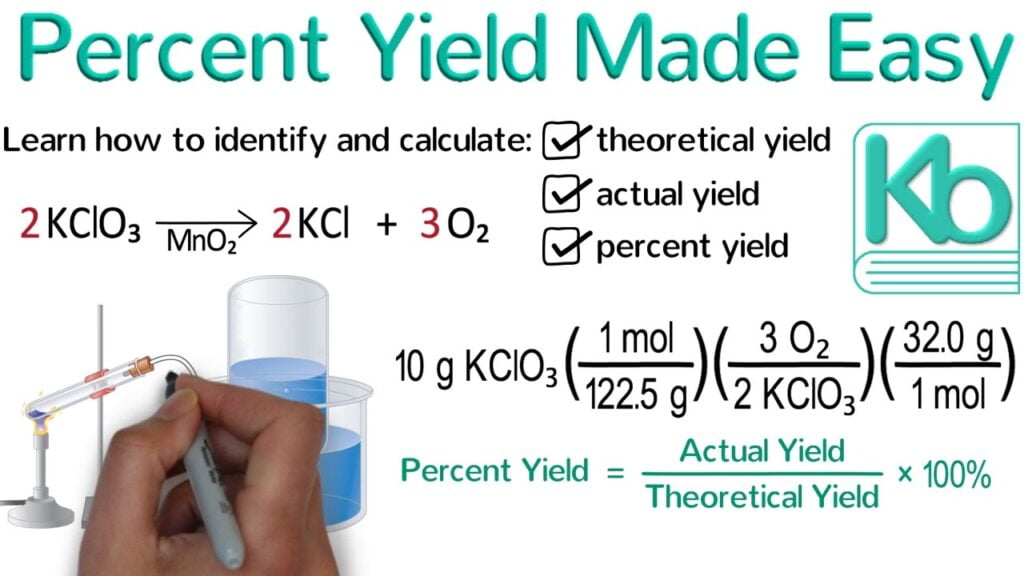
AI Assisted Fuzzy Logic PID Control®.
Artificial intelligence assisted Fuzzy Logic PID control are one of the most important function on the word’s best practice approach on BGA Rework Station world.
Normally, the Fuzzy Logic PID control alone are the best ever practice approach to control in close-loop the temperature over a BGA / chip.
As the Fuzzy Logic PID control are enhanced with the probe and error from all over the world where are used, our software, will push over all imaginable frontiers, the finest ever, best practice approaches for 100% yield, 100% repetitively rate. That mean that a BGA / chip rework process result in New-York will be the same in Tokyo, Bombay, Madrid, Vienna and so on… 100% yield, 100% repetitively rate.
AI Assisted Fuzzy Logic PID Control® - 100% yield, 100% repetitive rate
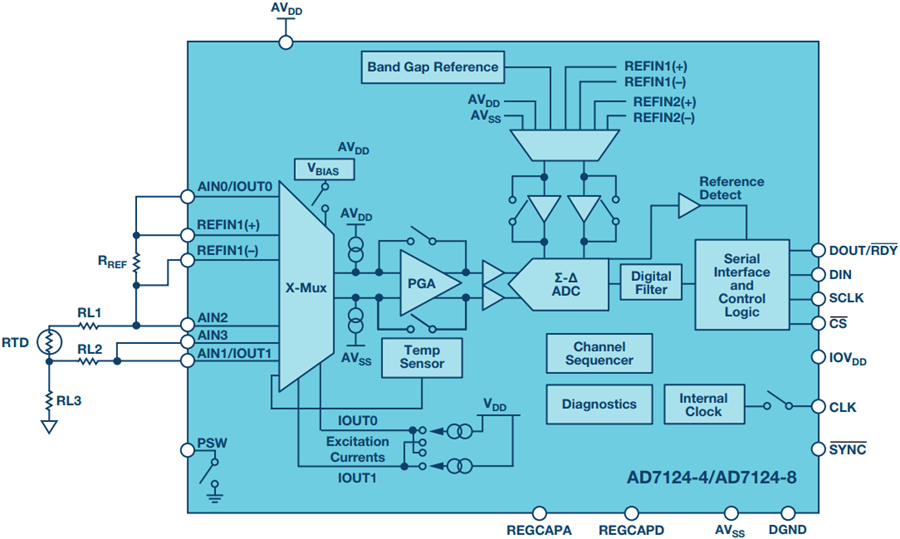
Dynamic Compensation®.
I’ll use the world’s best temperature sensors, both for contact and non-contact-IR sensors. The same sensors are used by NASA on his own projects. But…
When the sensors came from manufacturers arrive with some small errors (little less accuracy) about 0.5 °C, and that it don’t like to me. Well… As I have a NIST traceable certificate temperature measurement system, I’ll recalibrate them all. So…
Not only that the electronics hardware it has integrated “cold junction compensation”, “three points compensation table” and so on… But the used sensors are recalibrated with a NIST traceable certificate system as witness. That assure the veracity of the compensation parameters.
With that recalibrated sensors, later in Rework Process, are calibrating the non-contact sensors against the famous Object Emissivity factor.
In that manner, I’ll achieve less than 1 °C with a non-contact-IR sensors, Object Emissivity Factor… independent. In that manner can be exceeded this ugly term… Object emissivity factor.
Dynamic Compensation® - less than 1 °C error accuracy.
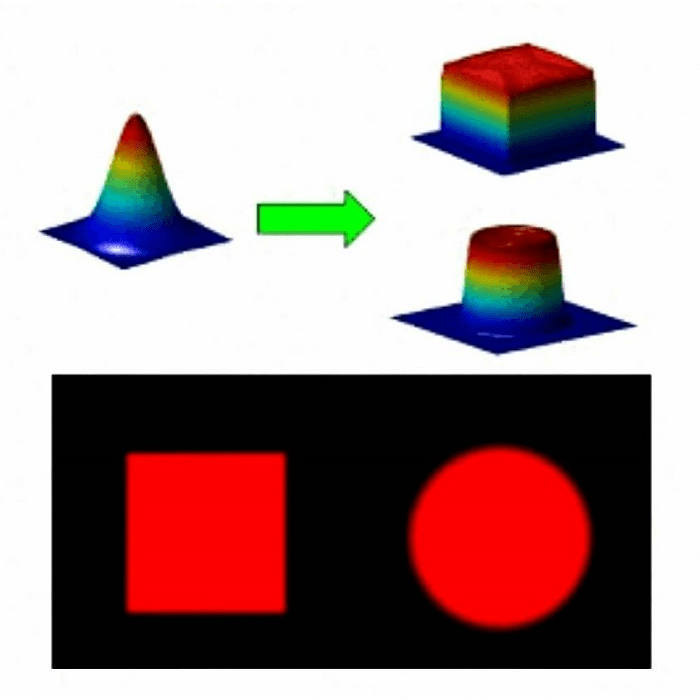
Perfect Diffused®.
As you know, the elliptical reflector have two focus points. One are used to place the emitter device and second point where the “focus” are reflected. Well…
That second focal point have a Gaussian shape. That fact is bad. On the left upside of the image, you’ll have a Gaussian beam shape. That shape has high intensity in the middle of the beam and much lower intensity in the margins (arrow like shape), that mean nonuniform beam distribution.
Using some high-tech processes, I’ll diffuse that high energy from the middle, equally dispersed all over the BGA / chip area.
That diffusion process assures that the entire area of BGA / chip receive the same amount of energy to transform that electromagnetic energy in heat (self-heating). Later from software timings that self-heating process are controlled in that manner, that the transversal thermal inertia are exceeded, in that manner assuring a perfect temperature uniformity over entire array.
Perfect Diffused® - Near to perfect uniformity across BGA / chip - 1 °C
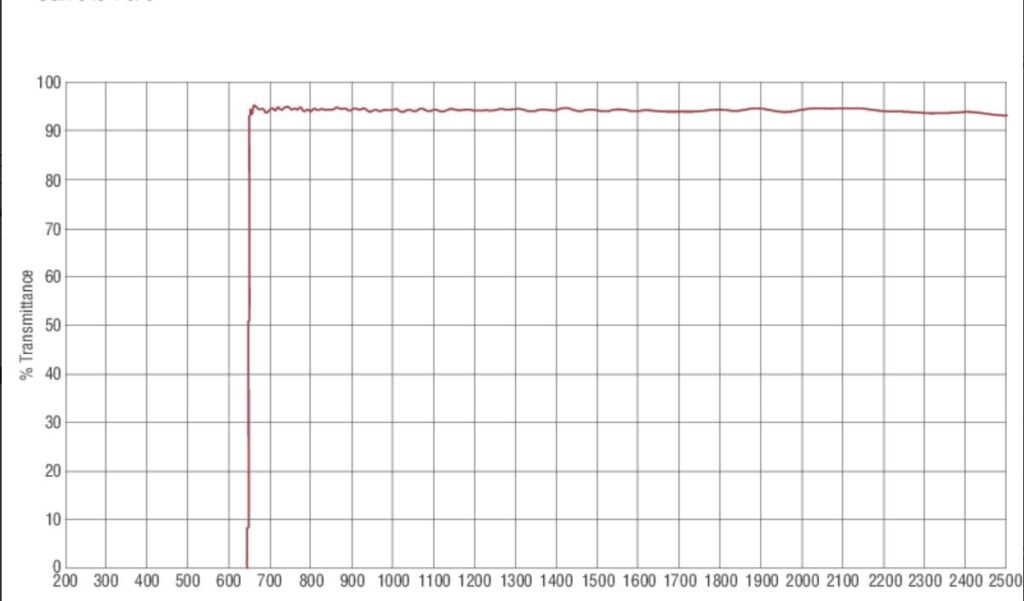
Red Pattern®.
As you’ll see in the above image, I’ll cut the visible light on 645 nm. In this manner, remain some red part of the visible spectrum of electromagnetic energy (red light) that are clearly seen, for accurate knowledge where the emitted electromagnetic energy touch the surface of BGA / chip.
In the image, you can see that from 645 nm to 2,500 nm I loose only 5% of energy. Furthermore, In practice, I think that I lose less than 5% of energy due to the fact that at highest power the long pass filter remain cold.
Red Pattern® - Perfectly seen where the energy touch the BGA / Chip.
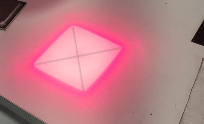
X Mark®.
As you’ll see in the above image, a black X cross appears on the red square shape.
That black X is used to clearly see when the diffused pattern on the image are perfect focalized (please do not confound with focussed). That functionality is a big visual help when the beam shaping is in manual mode. On that mode, you have the possibility to manually alter the shapes of the electromagnetic energy beam and is a must-see when the focalized of the image is in the right value.
X Mark® - a must-have to see when the beam spot is focalized.
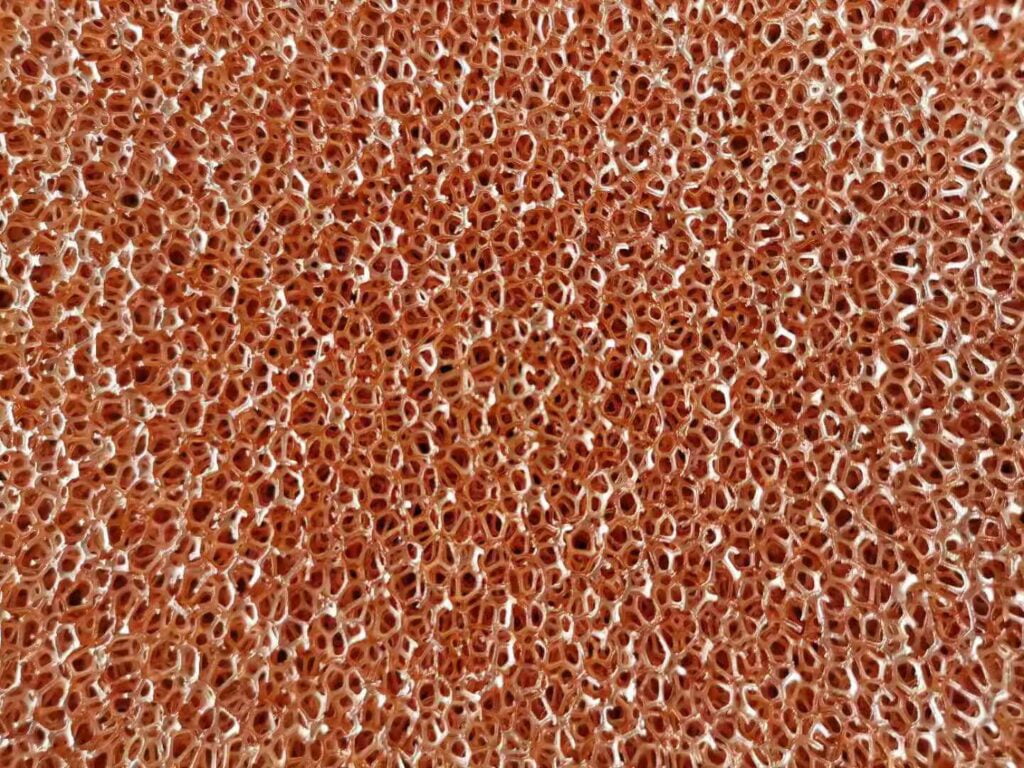
Cool Control®.
The combination of highly reflective (lowest absorption of heat), surface of cooper reflector 97%-98% (in some case gold-plated), with open cells copper foam on backward side of the reflector assure the best reflectivity combined with the highest possible heat radiant surface that copper foam it has.
That approach combined with a large (80 mm) ultra quiet / high speed fan assure a cool functioning of the Direct Energy Generator.
Cool Control® - coolest possible functioning best practice approach.
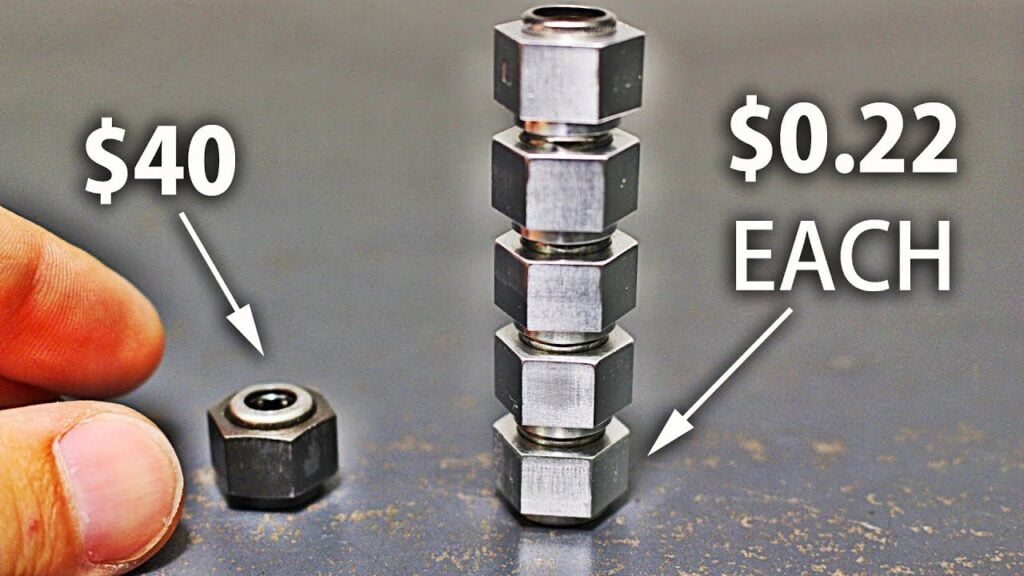
Gold Cheap Spare®.
As many other electronics device, My project of real Professional BGA Rework station have some consumables. For example, the Pure Electromagnetic Energy generator it has some consumable parts after 60 to 400 hours of functioning need to be changed.
All parts that form that generator pay a special attention on that consumables parts that must be relatively cheap to change with a new one.
Gold Cheap Spare® - cheapest possible spare-parts consumables.
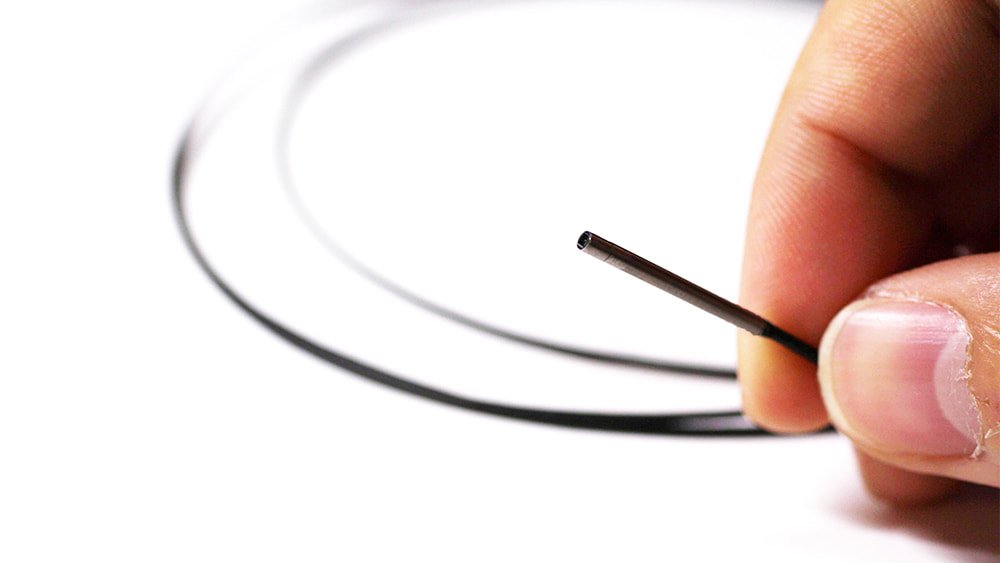
Closeup Process Visible - view Camera®.
A closeup process view camera in visible spectrum of light, it is a must when we’ll speak about accuracies of the Rework Process.
Unlike “well-known, professional, Chinese” manufacturers that situate that type of camera at huge distance from objective (BGA / chip) process, I’ll situate the smallest possible camera High Definition (> 5 Mega pixels) very close (about 10 mm) distance from BGA / Chip Rework process.
With this approach, I’ll eliminate all possible disturbance / errors in the Rework Process view.
Closeup Process Visible - view Camera® - best practice positioning.
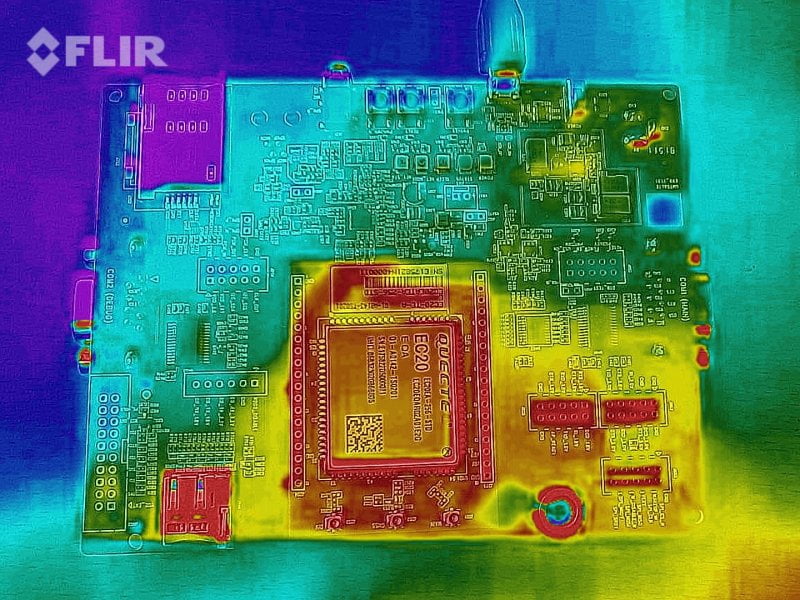
Closeup Process Infrared - view Camera®.
Another must-have on the best practice approach, is the IR-camera. This camera has a crucial importance on the velocity / inertia of uniformity dispersion of the heating among entire BGA / chip.
It is a must-known, real-view temperature gradient across the entire array of BGA / chip that are subject to Rework Process.
The timing of heat propagation across entire superfine of BGA / chip, are clearly visible with eyes and completely processable by hardware / software of a Real Professional BGA Rework Station. In that manner, a first time Rework Process are perfect.
Closeup Process Infrared - view Camera® - a MUST have camera.
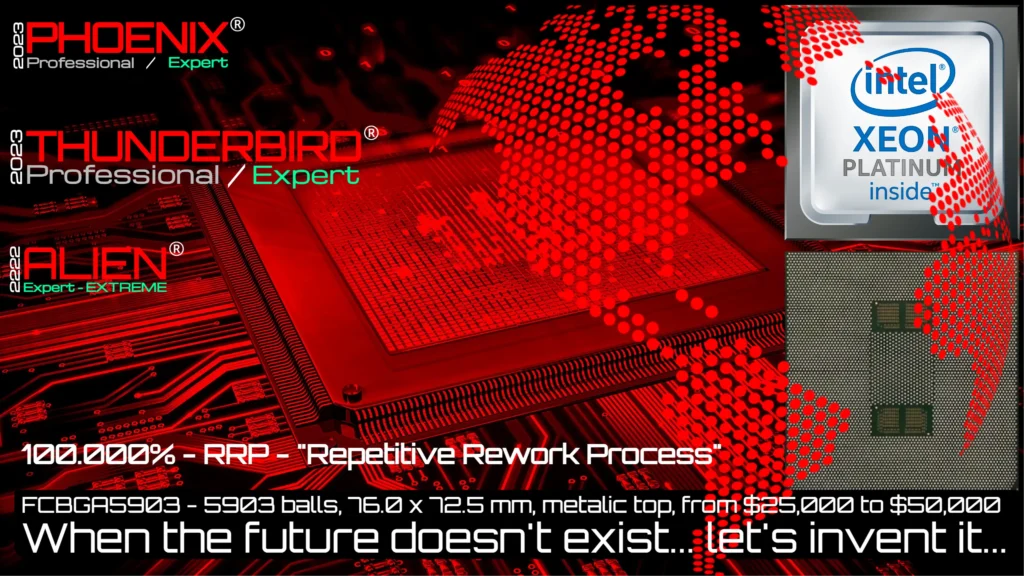
Top Heater / temperature reading / temperature control - the most important... Of a Real Professional BGA Rework Station.
Add Your Heading Text Here
At a simple look to a real Professional Rework Process / a Real Professional BGA Rework Station, we can distinguish two most important parts that form / contribute at our Real Professional BGA Rework Station / Rework Process.
- Bottom-Heater
- Top-Heater
From what we can read on above, two point… Seems that is an easy task. Well… I’ll inform you that is not an easy task. The “well-known, professional, Chinese” manufacturers, for more than 35 years, try only errors, the worst practice ever approaches, pseudo-scientific / pseudo technologies approaches. They continuously intend to implement the pizza, popcorn machines, Santa Claus cousin on one of the highly complex / highly qualified process.
That approach doesn’t work. All over the internet, in forums, on wiki’s… They cry after that buy one or more piece of that garbage that the “well-known, professional, Chinese” manufacturers are selling on past / today market.
From what I saw on internet, seems that I’m the only one person that chose NOT to buy garbage from that market, I’ll choose to do a huge Research and Development work, to achieve a truly / real Professional BGA Rework Station.
As I say before, here it is only some theoretical part from my Research and Development about my vision / what I discover over the last 10+ years from my first contact with this subject. The practical approach you can follow here, on the sister website of that website… BGA-Rework-Station.com (click or touch the link).