Best practice PCB / board policy. Temperatures, accuracies, elasticity, control, electromagnetic energy... and more...
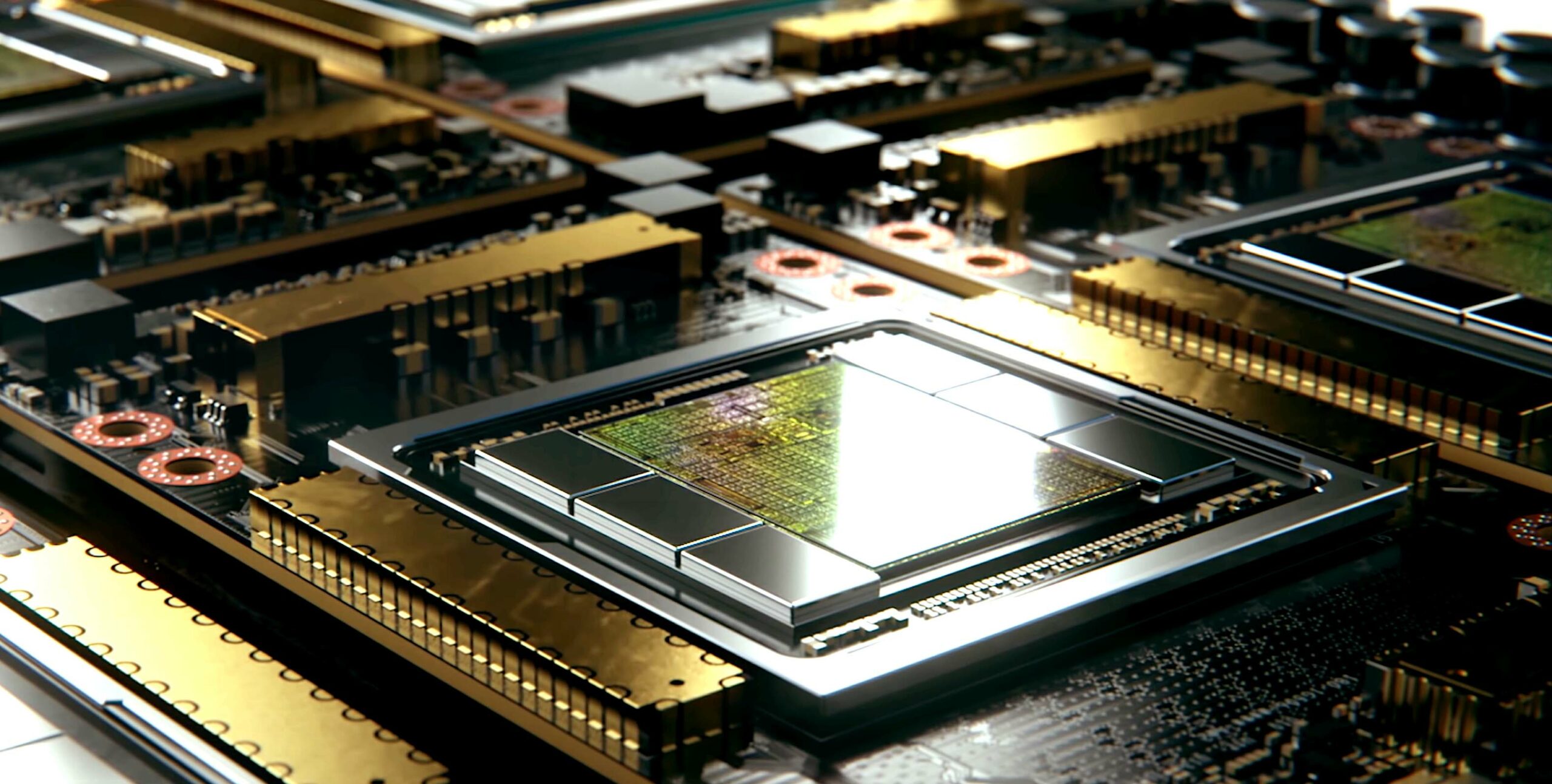
When we speak about best practice PCB / boards on BGA Rework Stations or Rework process, we need to know some important facts that we MUST respect. Below we'll speak about materials, temperature, Tg - point, FR-*'s, VIAS, uniformity and more. Please read carefully all information.
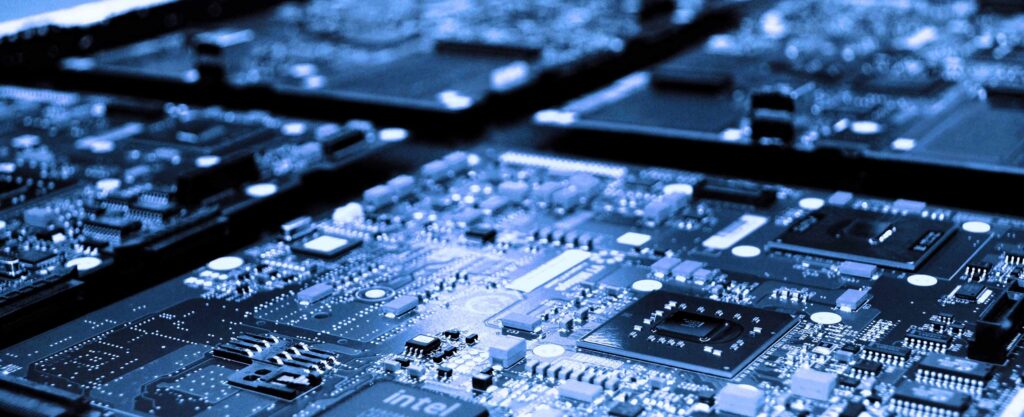
Add Your Heading Text Here
A PCB / board seems that is strong, seems that it is indestructible. Wrong. A PCB / board are a delicate object, very sensible at many factors. If we do not respect some common sense / best practice PCB / board, the PCB will break. Nowadays, many of PCB's / boards are cheap and even not worth to be serviced / repaired / fixed, but another, huge amount of them have a high price, So... It is worth to be serviced / repaired. To fix that PCB / boards that worth our attention, many times we need a highly specialized tool, a BGA Rework Station.
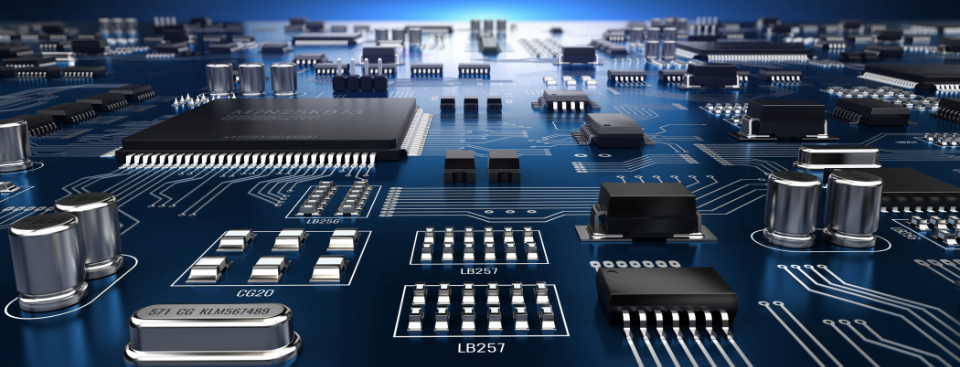
Add Your Heading Text Here
The PCB / boards are manufactured in many countries, any manufacturer have his philosophy about the textures, colors, materials and so on when manufacture a PCB / board. In fact, at nobody seems to import that aspect. For us, that attributes are very important. When we speak about BGA Rework Stations and best practice PCB, we speak about different methods to measure that temperatures. We can measure that temperatures by contact sensor / thermocouple method or in non-contact IR sensor method. Texture, color and materials have a high impact when we measure temperature.
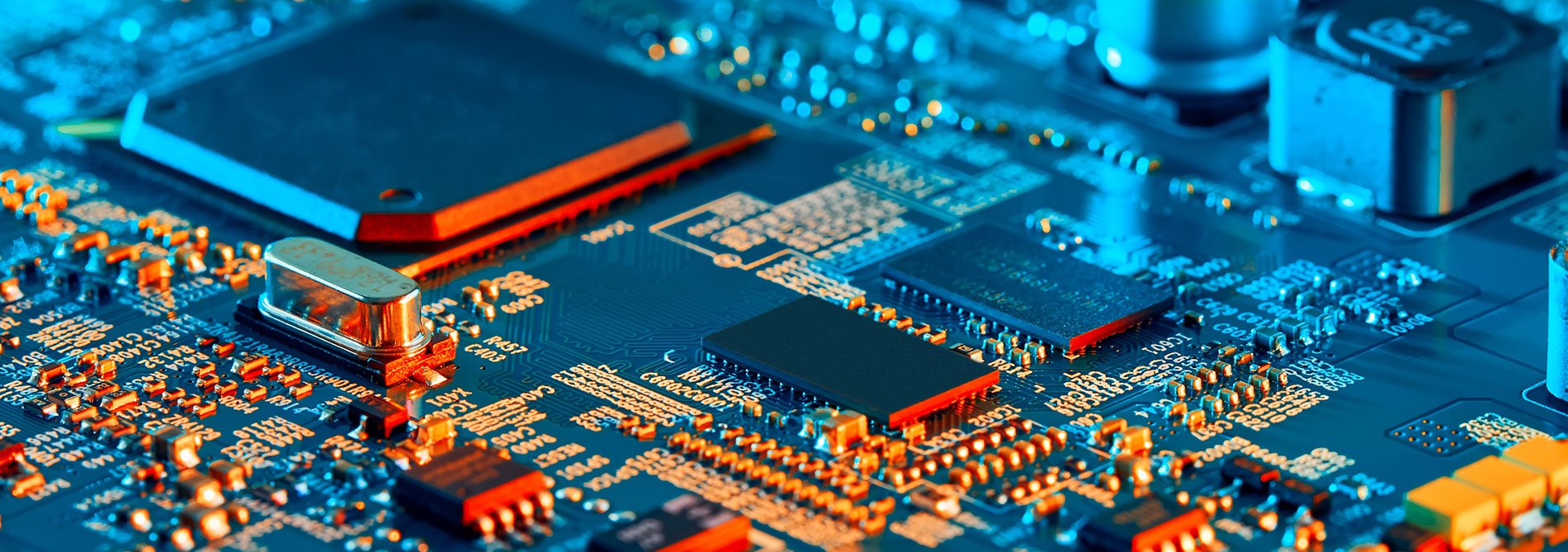
Add Your Heading Text Here
Here we'll speak about the relation between BGA Rework Stations and best practice PCB / boards. Please pay attention to the fact that nowadays, independent of amount of money you have on your inversion budget, you don't have to buy a real professional BGA Rework Station on the market. Here we'll don't speak about what "BGA Rework Stations" can do relatively to PCB / Board. I'll speak about the best / common sense practice that you MUST respect when you work with a BGA / board that deserve to be fixed / repaired. So... Let's Rock...
What we need to know about best practice PCB's / boards. Why we need to pay a special attention to materials, temperature, Tg - point, FR-*'s, VIAS, uniformity and more?!
Let's speak about materials and why the materials have so importance in BGA Rework Stations and PCB / boards. About resins, glass fiber, ceramics PCB / boards, copper, vias plating, vias protection, masks, texture.
I’m a guy that come from a highly specialized / qualified electronic service field. Years ago, when I’ll was short in money, I’ll was obliged to buy my first multimeter (a Chinese, cheapest one). At that time, I know that worth nothing but… was what I’ll have at that moment. I think… when I’ll grow up (in money), I’ll change it. After a while, I’ll change it with a Fluke – 289. In that same time, I’ll was obliged to buy my first oscilloscope (a Chinese, cheapest one). At that time, I know that worth nothing but… was what I’ll have at that moment. After a while, I’ll change it with a Fluke – 190-202 SCOPEMETER.
On the same path as above, I want to buy a BGA Rework Station. At that time for me was a MUST-have. I’ll do a search on the internet for a Chines’ garbage – I’ll fund… nothing. I look at “well-known” / “professionals” manufacturers… First that I’ll see was the garbage unjustified prices for same worst approach, and the fact that are same miseries like Chines’ manufacturer’s worst approach. So far so good… But I need a real Professional BGA Rework Station. What can I’ll do ?! I’ll wait… For some years… Meantime I’ll study from scientific / technological point of view, best approach. That was between 2012 and 2017.
I’ll wait until 2017. In that year was enough waiting. In that years, between 2012 and 2017 I loose a huge amount of money due to the fact that I’ll don’t have a Real Professional BGA Rework Station. But I learn so many things in physics, material technology, best approaches and so on… in fact I learn / understand what I need from a real Professional BGA Rework Station. On 2017 still, I needed A Real Professional BGA Rework Station. On 2017, I’ll start few projects about BGA Rework stations, from two points of view – worst practice ever (all “will-known”, “Chinese”, “Professional” manufacturers) and worst practice – science / technologies / logics / electronics (click or touch to go).
In 2017, after that I’ll see that all “well-known”, “professional”, “Chinese” manufacturers does same things – copy / paste same errors, same aberrations, same worst practice ever… I decide to put in practice all my results derived from my past researches. I probe / test from theoretical and practical point of view, all and every worst practice / approach ever that all manufacturers use. That worst practice / approach ever, MUST not be used on electronics, on BGA Rework Stations. Below you’ll have my theoretical / practicals that I’ll discover about worst practice approach that all “well-known, professional, Chinese” have.
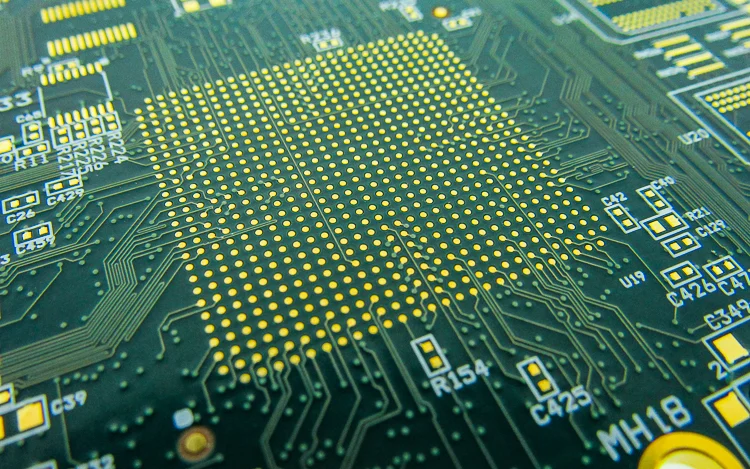
Resin + glass fiber PCB / boards. This type of materials are most used on fabrication of PCB’s / boards due to the fact that bare cheap. Been so cheap are widely used from DIY project, prototypes and final highly complex products. I have some god / bad attributes. One of the best attributes is that this type of PCB’s / boards it has a highly electrical insulating propriety (In our case is not important). What it is important is the fact that fiber-glass resin PCB’s / boards have highly thermal insulation propriety. That is mean as best practice PCB, take in account that the heat need much time to be propagated among the board.
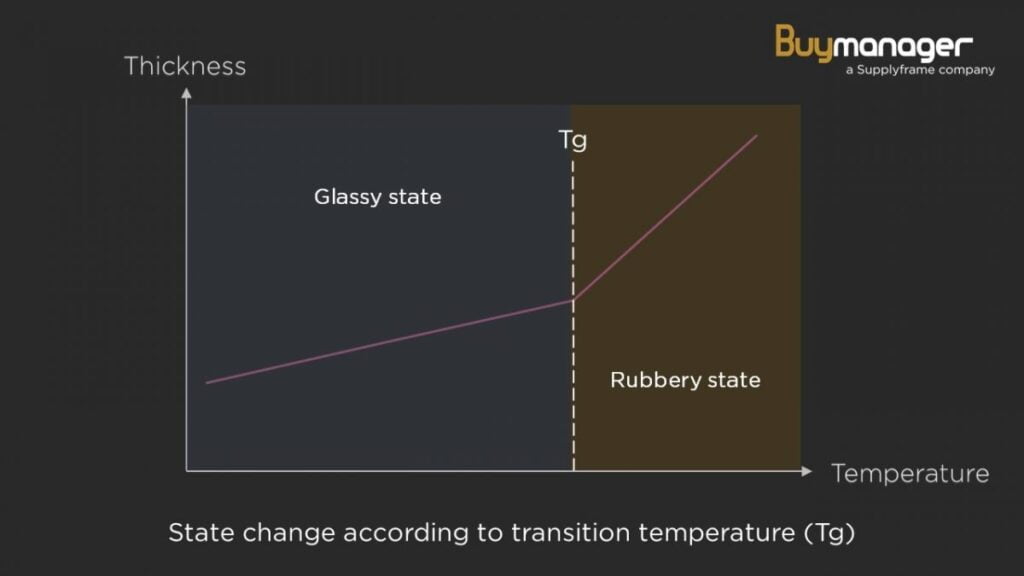
Another best practice PCB that must know is the propriety for that type of PCB / board are the fact that can have two states. At room temperature, a PCB / board are hard, not like a real glass, more like a hard plastic. As we heat up the PCB / board, It looses that glassy like hard propriety and become more and more soft. At one moment, if the temperature is high enough, The PCB / board completely loose glassy like hard propriety and change the state from glassy like to rubbery like, state. So… As we heat up the PCB / board, it is changes it hardness, from glass like state to rubbery like state.
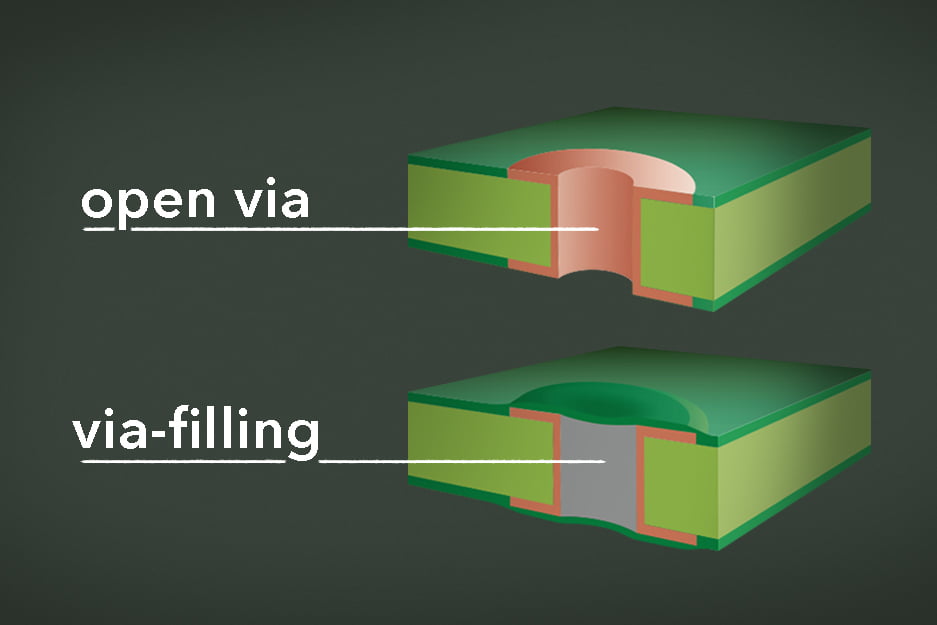
On best practice PCB board, let’s speak about the VIAS. VIAS are that small holes without any component in them that make electrical contact between various layers of the PCB / board. Normally are made from copper (copper plated blind or not holes). That copper plated are very thin in layer, so… are very delicate. Sometimes that VIAS are protected with mask materials, sometime with tin. Tin protected vias are the hardest version of vias. Generally, nowadays due to a bad behavior of the PCB / boards manufactures, tin protection are not used. So… normal vias are very delicate and too much thermal stress almost sure that will break some.
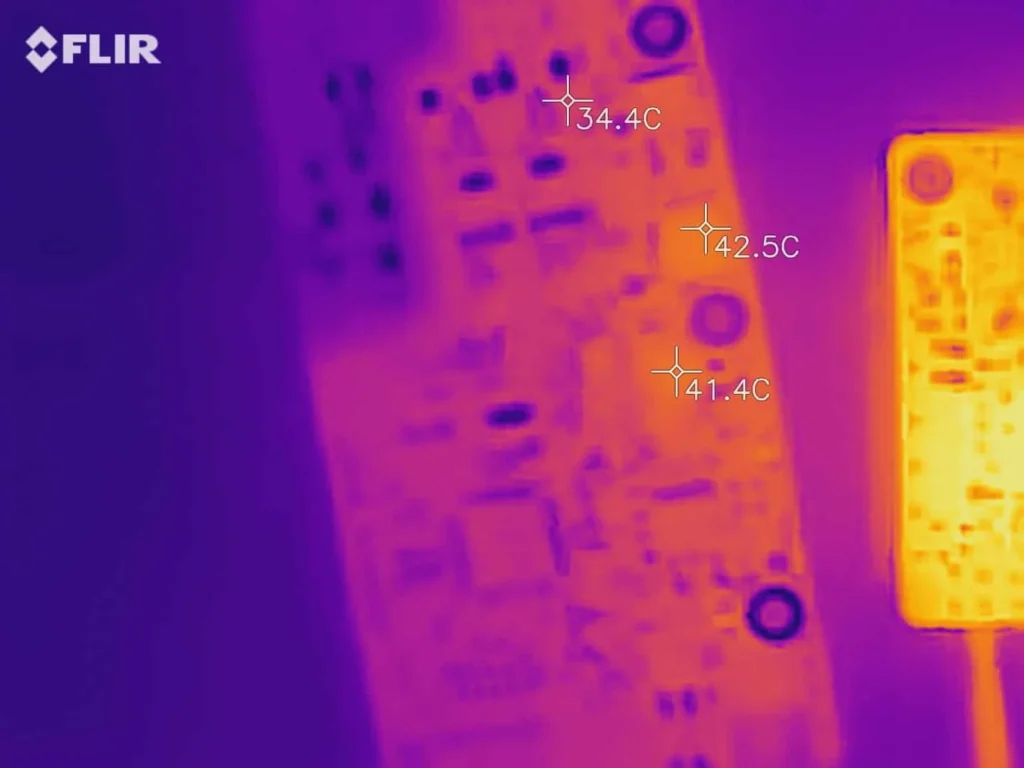
For that reason, we need to take our time when we heat, with best practice PCB / board approach. We need to respect the big internal thermal inertia of PCB / board and gibe it mandatory time to uniform propagate the temperature constant in the PCB / board material. Another huge attention that we MUST pay is to oxide remover / anti oxidant flux / paste that we use. That flux / paste MUST not oxidize himself and the pads from PCB / board on the heating time process.
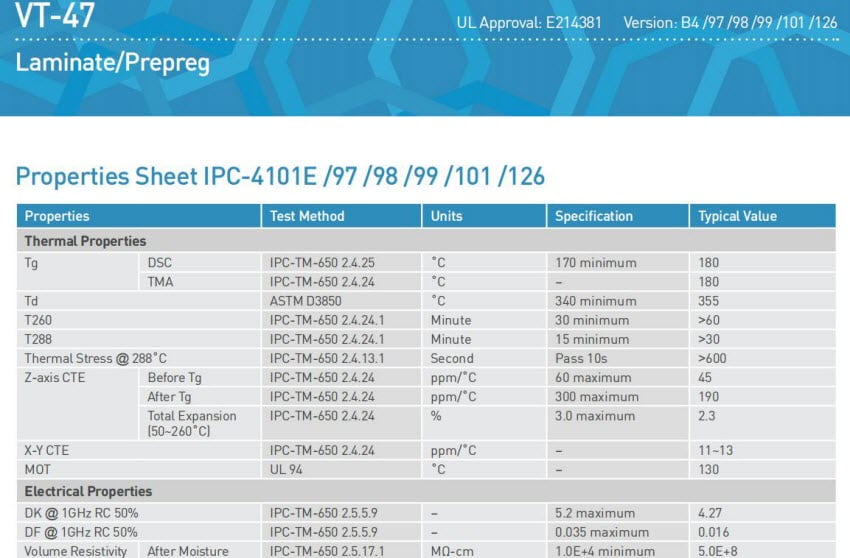
For that reason we MUST that never, ever can’t go over the minimum T-g -point that we know (110 °C) for the best practice PCB / board approach. We never ever go to the rubbery state of the BGA / board to avoid unnecessary stress over the VIAS. As the chain theory say… “the chain will break at the weakest link”. Our weakest link on this case is the VIAS copper platted holes.
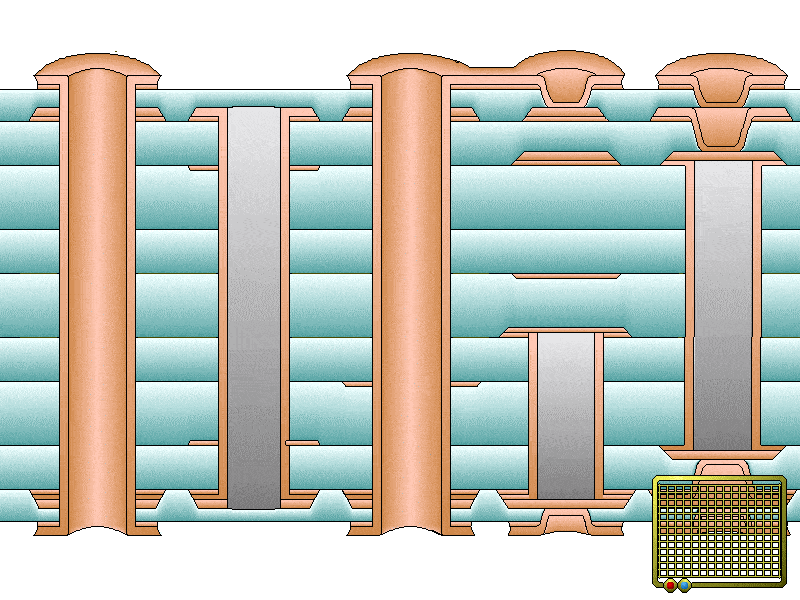
Another thermal dependent attribute that PCB / boards have, it is the comportment when it is heated. All material on this planet, when the temperature change, vary it shapes. That shape variation can be simply expressed as dilatation and contraction. When we heat a PCB / board, that board will dilate. When we cool that board, it will contact. We can express these two proprieties in expansion and contraction as attributes. These attributes are very important. When we heat a PCB / board, we need to pay attention to expansion / contraction factor.
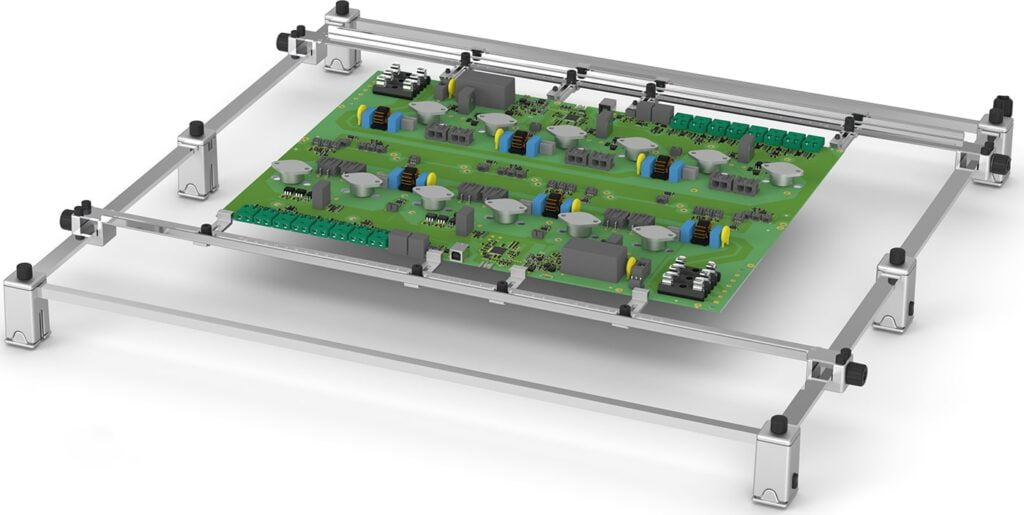
As best practice PCB / board approach, we need to take in account the PCB / board expansion, assuring that the support of the PCB / board are slightly expandable / elastic. That comportment assure that when the PCB / board will dilate / expand, will have enough space to do it and do not bend. If the PCB / board maintain the plane aspect, we will have a perfect plane surface to mount our BGA / chip.
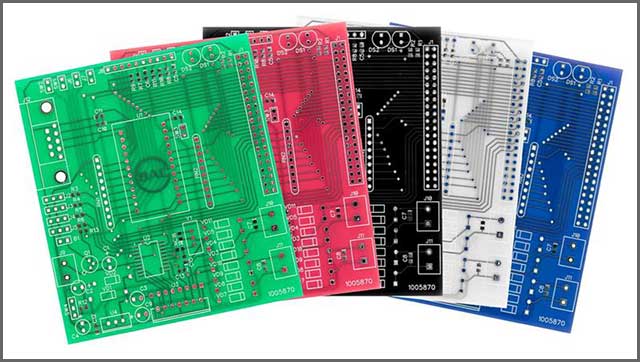
Also, the texture, color, materials have a huge importance as best practice PCB, when we choose the method to heat the PCB / board. In fact, we need to choose the best heating method to be sure that we respect the best practice PCB / board principles. None method of direct heat transfer (convection / hot air or hot gas – nitrogen), “Black-IR” can be used. Remain only the radiation method as best practice PCB / board. That mean that the only method that can be used to heat a PCB / board are to radiate the PCB / board with some electromagnetic energy. Here come the problems.

When we choose the part of electromagnetic energy to transfer / radiate, the PCB / board, as best practice PCB, MUST be paid a special attention on harmfully energy for human body (X-rays, microwave energy like). That energy MUST do not be used. So… If we want to respect the best practice principles when we heat a PCB / board, we must choose a type of energy cording to what I write above and below, the electromagnetic energy spectrum that remain at our disposition still are wide, so we have from and how to choose the right type.
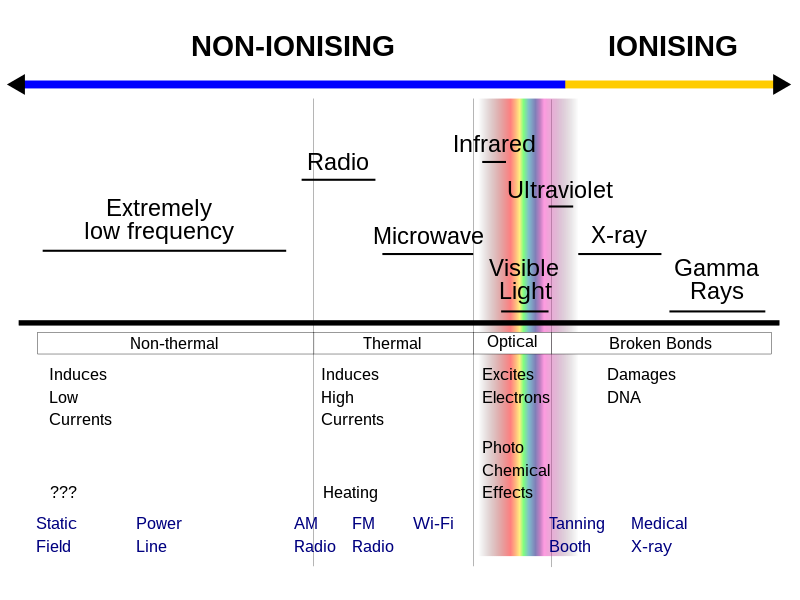
The electromagnetic energy spectrum is so large (from audio to gamma rays), that it is a real problem, as best practice PCB / board, in our choice on what part of that energy we’ll use to radiate the PCB / board. Our problem is that the part that emit this electromagnetic energy MUST be at enough distance from PCB / board that do not affect the PCB / board temperature. It means that direct temperature transfer (convection) MUST be minimum between electromagnetic energy emitter and PCB / board. Due to this fact, all energy below SW-IR MUST be avoided, MUST not be used.
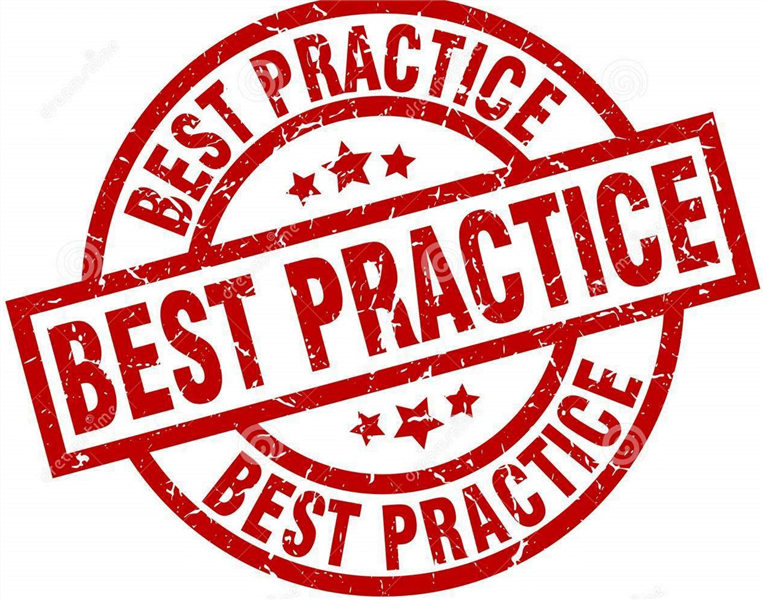
If we conclude … we can write a paragraph about best practice PCB / board heating.
As best practice PCB, due to attribute that have the materials from which are manufactured a PCB / board, we need to avoid high inertia, know the Tg – point. Avoid with all price the thermal stress, pay a special attention at elasticity of the support for PCB / board. We need to use both, contact sensors and non-contact IR sensors and / or thermal camera, we need a method to compensate temperature coefficient for an accurate temperature measurement. The electromagnetic energy MUST be chosen carefully between MW-IR and UV.
Just like in above best practice PCB, the control of electromagnetic energy that are used to irradiate the PCB / board MUST use PID / Fuzzy Logic PID / AI assisted Fuzzy Logic PID. All that, for an accurate temperature control according JEDEC (are not the best ever practice but for the moment we don’t have another) standards. A special attention MUST be paid to the fact that the PCB / board MUST do not heated with the convection method (direct transfer of heat between temperature emitter and PCB / board). MUST be used the radiation method at enough distance.
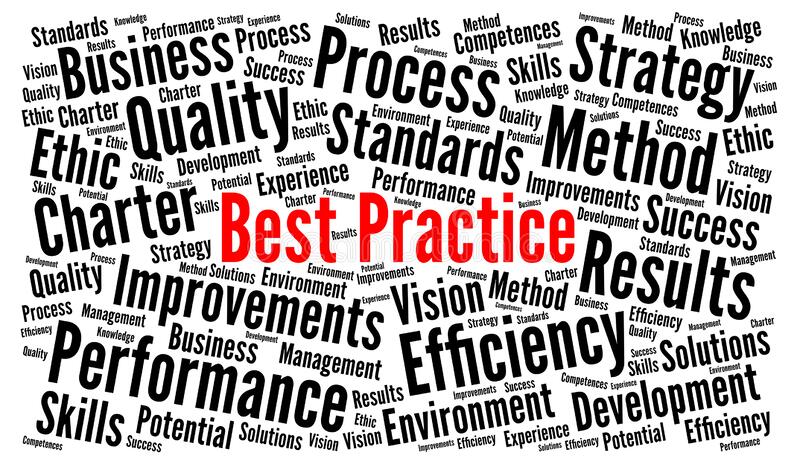
- From a general best practice PCB / board point of view, we need many individual best practice PCB / boards.
- Highly thermal insulation propriety – heat need much time to be propagated among the board – high inertia.
- Not oxidize himself and the pads from PCB / board on the heating time process – Flux / flux paste.
- Heat up the PCB / board, it’s change the hardness, from glass like state to rubbery like state – Tg – point.
- Vias are very delicate and too much thermal stress, almost sure that will break some – thermal stress.
- To heat a PCB / board, we need to pay attention to expansion / contraction factor – elasticity.
- Texture and materials have a high impact when we measure temperature – contact sensor.
- Texture, color and materials have a high impact when we measure temperature – non-contact IR sensor / camera.
- Accurate temperature measurement.
- Accurate temperature control PID / Fuzzy Logic PID / AI assisted Fuzzy Logic PID.
- Electromagnetic energy above MW-IR, nothing below MW-IR.
- Electromagnetic energy Below X-rays, prohibited electromagnetic energy in X-ray spectrum.
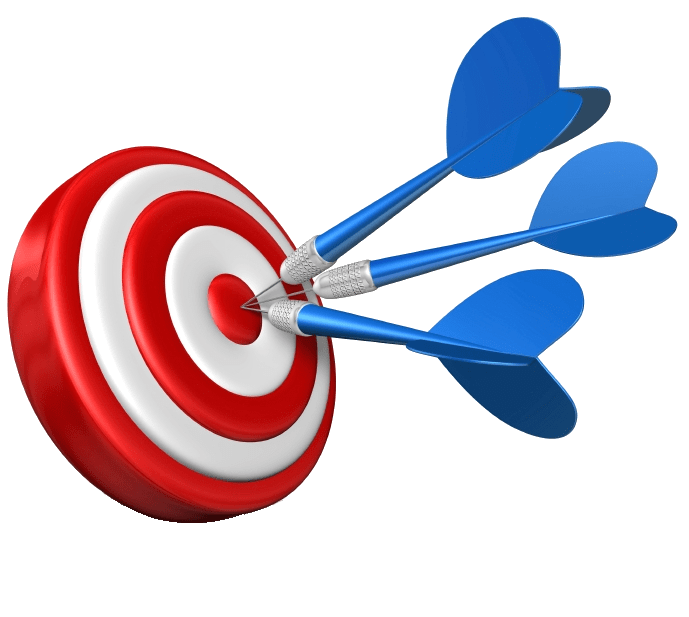
That approach is the only one approach that clearly use best practice PCB / board and assure us a complete / accurate control over the best practice PCB / board heating process. Also, that approach gives a high conversion rates between consumed power and heat generated, with a minimum about 65-68% and a maximum of 85-88%. We can compare that percentage with the percentage that hot air / hot gas (nitrogen) it has (about 10-15%) or “Black IR” 25-30%. With irradiation method, not only that we have best / complete control over heating process, but we have an important energy saving percentage – 30-70%, that is a huge amount.
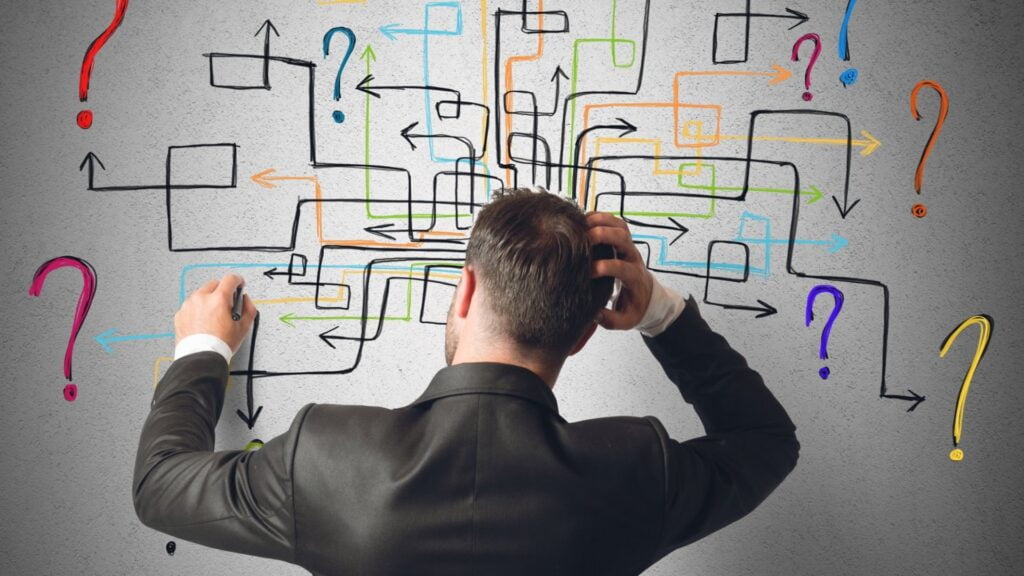
As you see on what I’ll describe above… Seems to be a tricky business, a complicated process, when only speak about PCB / board heating. That it is true. But if we use the science, the right / appropriate materials technologies, that tricky business, that complicated process, become a simple and normal approach, a general best practice, when we are speaking about soldering, selective soldering, BGA Rework. When we apply all the above to a bottom-heater from a BGA Rework Station, we’ll have a big part solved, from our project.
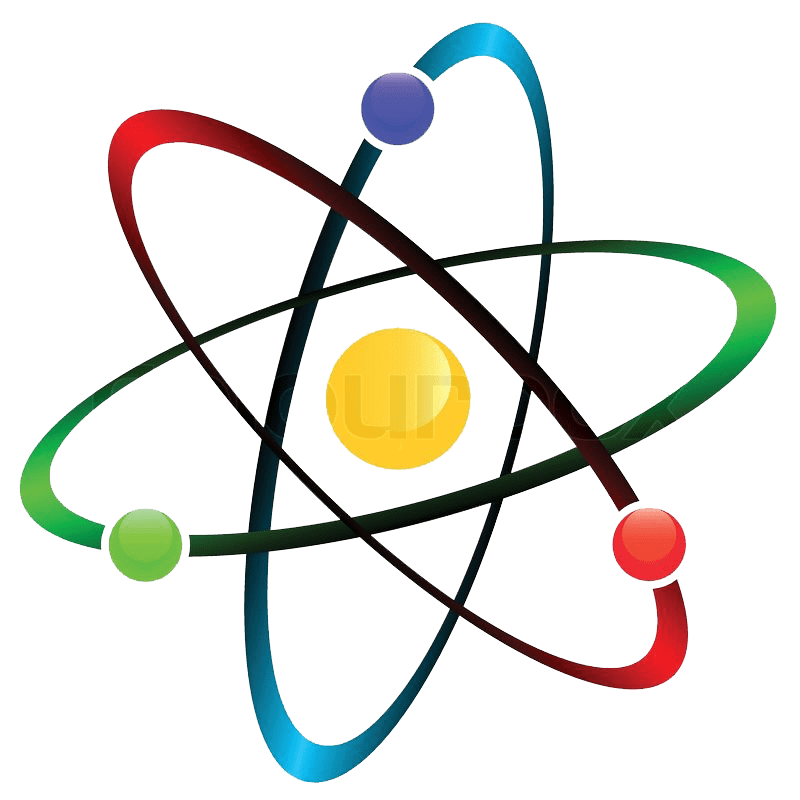
I bet that none of “professionals manufacturers”, “well-known manufacturers” even they don’t know about best practice PCB, about what I’ll write here. Did you know why?! Because here I’ll speak from scientific, technologies, best practice point of view. They do not understand that language, that you, the real professionals in electronics sciences, understand. The “professionals manufacturers”, “well-known manufacturers” only understand money language, understand pseudo-science, pseudo-technologies, the worst practice BGA Rework process ever (click or touch this link to go to west practice ever approach), cheating, liens. For them, the best practice PCB / board are useless. That is the only one explication for what they sell.
All what I write here from a theoretical point of view, about best practice PCB / board, I’ll test it from a practical point of view on the Alpha state of my projects. Click or touch to go to my projects. BGA-Rework-Station.com.
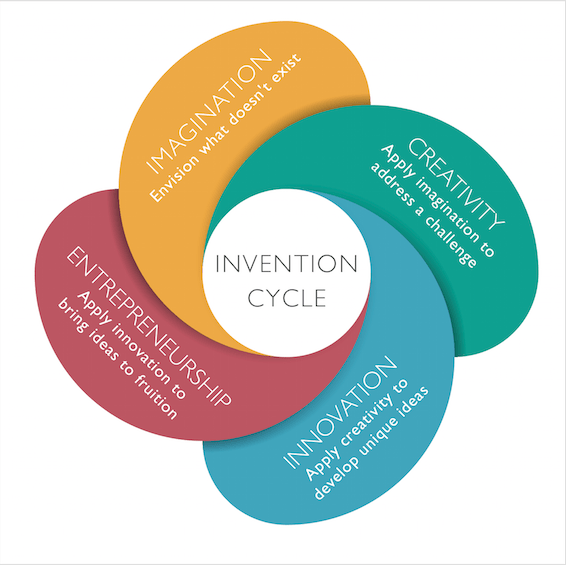
In the soldering part of the electronics / selective soldering, the past was bleak, the present is non-existent, the future is up to you. For many years, many technologies were invented and perfect compatibles with selective soldering. But the “well-known, professional, Chinese” are blind. They don’t see that technologies, and in fact… for them are not important, If they, with what it has at this moment, make money… Why change that recipe?!
Did you know that the electronic components to be soldered / reflowed on a PCB, about 1 m / 1 m (square) take about 5 minutes?!
If I’ll tell you that same process… can be made in 10 –15 seconds?! All that with technology invented with 15 year ago. I’ll don’t speak about 100 time less energy consumption… and more…
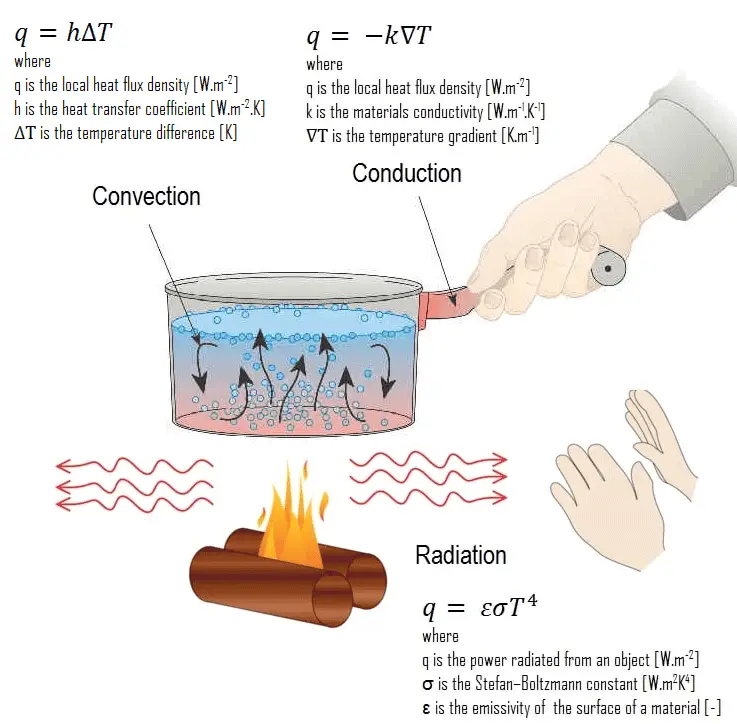
As a general best practice PCB / board approach, we MUST avoid heating a PCB / board with direct convection method. We MUST use the PCB / board radiation method. If we irradiate the PCB / board with appropriate method / electromagnetic energy, The PCB / board will absorb that energy and transform it in heat. The best example for this approach (irradiate with appropriate energy an object and self-heating that object), is the microwave oven. If we put a can with milk or a chicken or whatever any other thing that contain water or metal in a microwave, and we irradiate them with high power 2,4GHz wave…
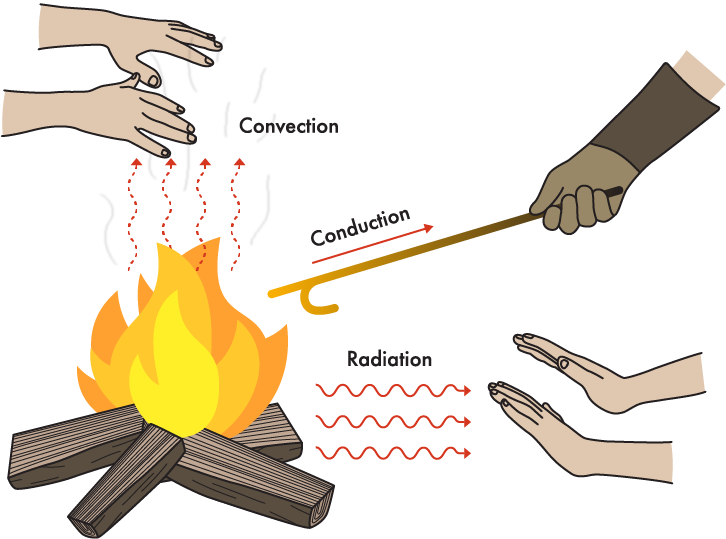
… That object will self-heating due to the water / metal vibrations molecules. The same phenomena appear in our case when we irradiate the PCB / board with an appropriate part of electromagnetic energy. The molecules from our PCB / board vibrate and generate the self-heating phenomena. That self-heating phenomena MUST be accurate controlled, the intensity of the radiated energy MUST be carefully modulated by a controller that use the best practice BGA / board concepts, accurate temperature control with PID / Fuzzy Logic PID / AI assisted Fuzzy Logic PID, algorithms.
So… due to the Google rule about paragraph… the conclusion about what I’ll write above about best practice PCB / board have fallen into two… paragraphs.
Worst practice approach takes you on the bet - on 0% yield / 0% repetitively rate.
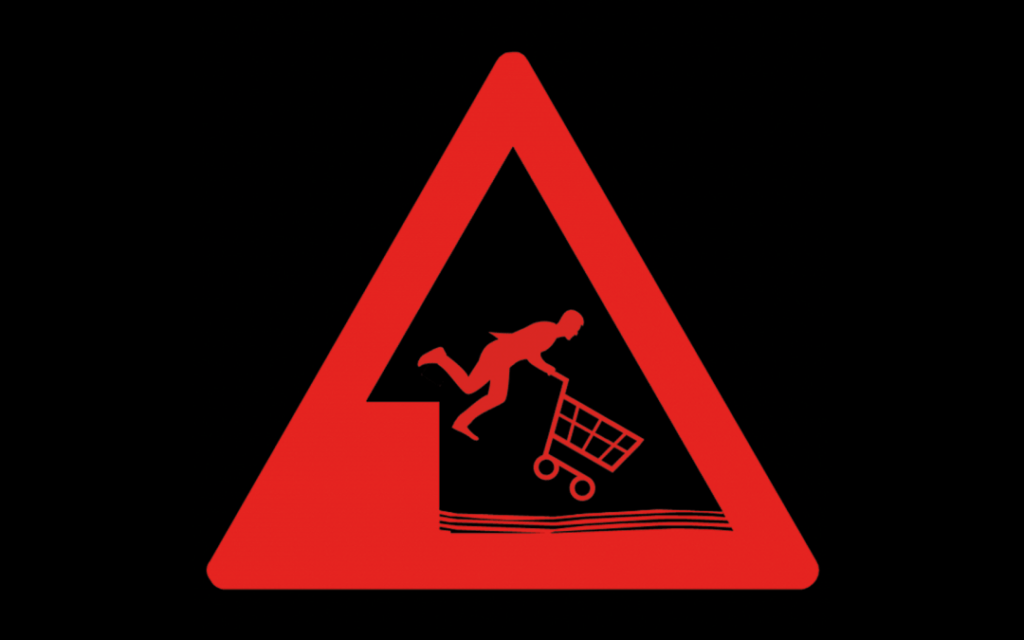
After that we read all information from this page, we can extract some conclusions about worst practice..
- The first and inevitable conclusion is that I’ll need a huge improvement for my English communication language.
- The second and inevitable conclusion is the fact that if we use the worst practice ever approach, we’ll go into bet games, where the chance to do a real Professional Rework Process are zero / 0. Even we will have some chance to solder some BGA / chips on the / PCB / boards, that doesn’t mean that the PCB / board will work. And if… the PCB / board will work… Well… never ever, we will have the warranty about how time will work.
- The worst ever, way / method / approach / practice that we use on PCB / board heating is an important factor that will have a huge influence on the quality of our BGA Rework
- We must think about all that is writing on that page, about all that are writing on that website and on the sister website BGA-Rework-Station.com
- If we don’t think, learn, understand, we buy with price policy, all that before buying a garbage, after that we will buy that garbage… we’ll pay.
- The worst practice ever approach, it is that we buy for price or whatever any other that scientifically, technologically approach, after that we almost sure we take in account that we’ll through the money to trash. Click here or touch, to read about the worst practice ever from PCB / board point of view.
Best practice ever approach takes you at 100% yield / 100% repetitively rate.
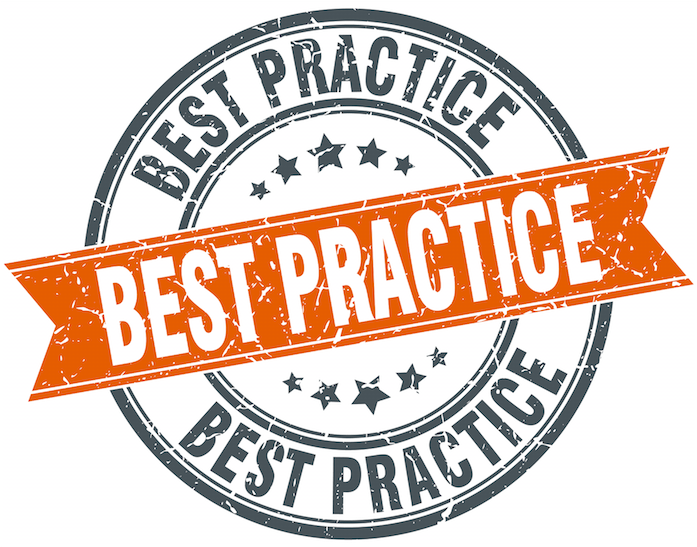
After that we read all information from this page, we can extract some conclusions about best practice..
- I promise that after that I’ll finish this draws, I’ll put all websites in the cleanest American language possible, I will ask somebody for that. Until that moment, if you speak science, technology, electronics… You’ll understand what I write here.
- It is a must to ignore all the worst practice ever approaches on that world. It is a must to put in balance all that “Well-known, professional, Chinese manufacturers” energumens manufacturers, that act like an amputated brain monkeys in his fight to sell us the worst ever pizza / popcorn machines or… Santa Claus cousin.
- We need to ask them to prove all stupid affirmations that they make all over the internet. We need to understand that an affirmation must be proved. Without proof, remain non-value affirmation, and we must avoid to pay attention to that.
- When we think, analyze, learn, document’s us before that make a considerable inversion, we not only are wiser, but we protect our pockets in front of without common sense, lairs, cheaters, that invade the most wide source of information… The internet.
Please, read with attention all information on this website and the sister website… BGA-Rework-Station.com (click or touch the link to go…). If you’ll see that message, I’ll work on that website to build them. Please be patient.